One misplaced item or a single inefficiency in a warehouse can cost a business thousands of dollars and hours of lost time. That's how crucial warehouse logistics is in today's fast-paced commerce environment.
A modern warehouse goes beyond a storage facility to a dynamic hub that is critical in ensuring that products get from manufacturers to consumers as smoothly as possible.
In this article, we'll delve into the package and boxes of warehouse logistics, and include practical tips to optimize your logistics processes.
What is warehouse logistics?
Warehouse logistics is at the heart of any supply chain, affecting everything from operational costs to customer satisfaction. A well-managed warehouse can give a business a significant competitive edge, enabling quicker deliveries and more efficient use of resources.
When you think about a warehouse, you might initially picture rows of shelves stacked high with products. While that's part of it, there's much more going on behind the scenes. Warehouse logistics is like a multi-layered cake, with each layer serving a specific function that contributes to the overall efficiency and effectiveness of the operation.
These layers (or core components) include:
- Inventory management
- Material handling
- Storage systems
- Order fulfilment
- Warehouse layout design
In this article, we will be breaking down each one for you to understand how they relate to your warehouse operations.
Inventory management
Inventory management is often seen as the backbone of warehouse logistics, and it’s not hard to see why. The only reason you have a warehouse is because there is inventory, and where there is inventory, there is procurement and order fulfillment.
Managing inventory is about maintaining optimal stock levels. But that's easier said than done. You're essentially juggling multiple variables—supplier lead times, seasonal demand fluctuations, and even sudden market changes, like a viral social media post that skyrockets demand for a particular item overnight.
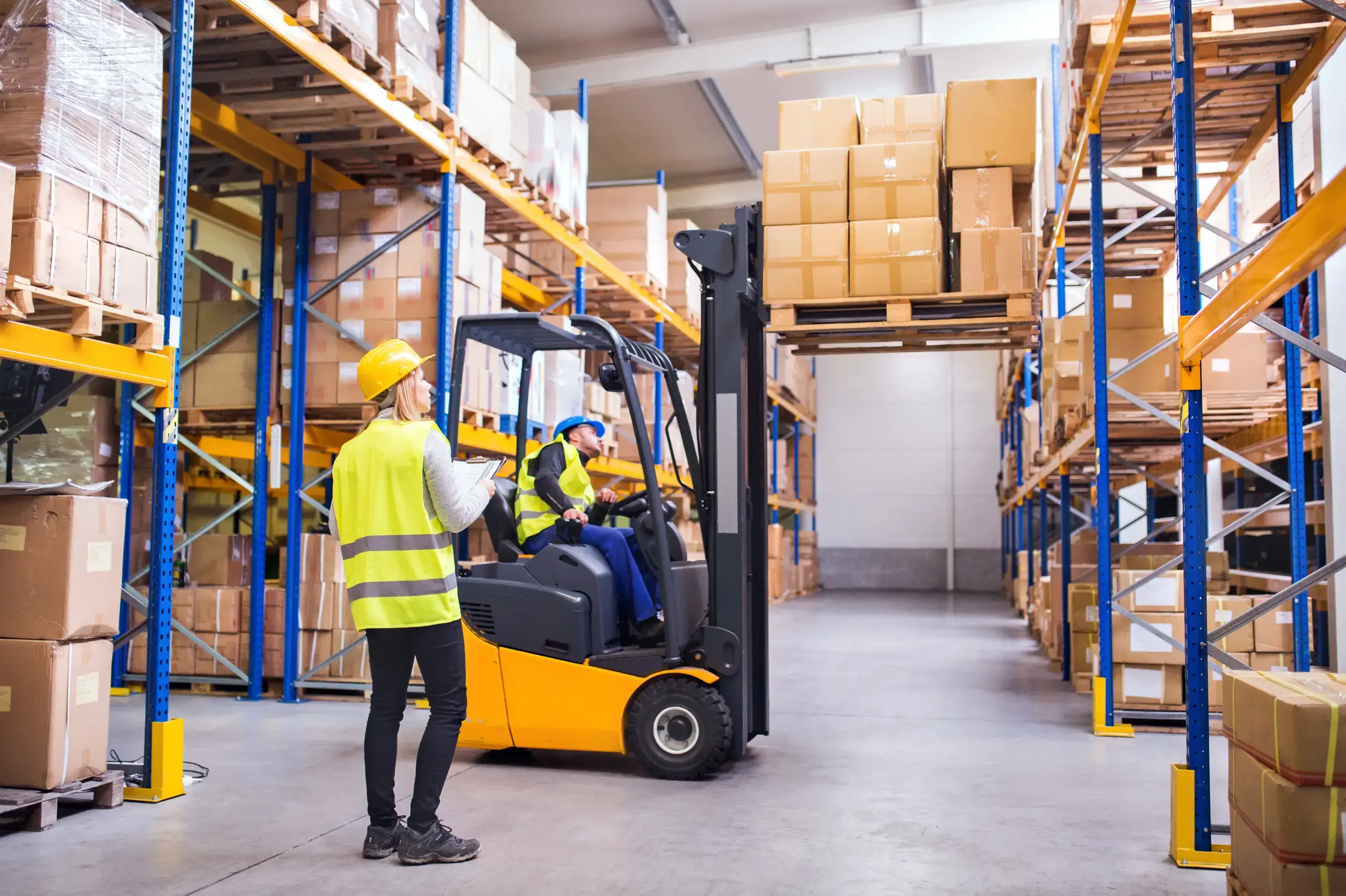
Imagine running out of a popular product during peak season. Not only do you lose sales, but you also risk damaging your reputation. On the flip side, overstocking increases storage costs and potential wastage. Managing your inventory effectively helps you strike the right balance, ensuring you have enough stock to meet demand without unnecessary excess.
As a business, you're also likely dealing with other types of inventory besides finished goods. Each inventory type has its own storage needs, cost implications, and turnover rates. For example, raw materials might be bulky and require special storage conditions, while finished goods might be high-value items that need secure storage.
Efficiently managing inventory also involves considering inventory costs. These aren't just the price of the goods themselves. You also have to consider:
- Holding costs: The cost of storing items, including rent, utilities, and security.
- Ordering costs: The cost of placing orders, which can include shipping fees and administrative expenses.
- Stockout costs: The cost incurred when you run out of stock, which can range from lost sales to long-term reputation damage.
Barcode scanners, RFID tags, IoT sensors and QR code generators are increasingly being used to automate the tracking of goods. These technologies not only speed up the process but also reduce the likelihood of human error.
One practical tip to optimize stock levels is to maintain a small buffer for emergencies or unexpected demand spikes. But be cautious—this isn't a license to overstock.
Material handling
Material handling is the physical movement of goods within the warehouse, from the receiving dock to storage areas and eventually to the shipping dock. It might sound straightforward, but inefficient material handling can lead to many problems—damaged goods, safety hazards, and operational bottlenecks, to name a few.
Material handling isn't a one-size-fits-all operation. It involves various activities and equipment:
- Receiving: The initial point where goods enter the warehouse. Efficient receiving processes set the tone for all subsequent activities.
- Transporting: Moving goods from one point to another within the warehouse. This could involve forklifts, conveyor belts, or even automated guided vehicles (AGVs).
- Storing: Placing goods in their designated storage areas. This is closely tied to managing inventories and warehouse layout.
- Picking and Packing: Retrieving items from storage to fulfill customer orders. This step is crucial for order accuracy and speed.
- Shipping: The final step where goods are loaded onto trucks for delivery. Mistakes here can be costly, as they directly affect customer satisfaction.
Consider incorporating technology like warehouse management systems (WMS) or automated guided vehicles (AGVs) to streamline material handling.
Storage systems
Modern storage systems in a warehouse are far more complex and specialized than unending rows of shelves. A well-designed storage system holds inventory, maximizes space, improves worker efficiency, and even enhances safety.
Storage systems can vary widely depending on the types of goods you're storing and the space available. Here are some common types:
- Selective racking: This is the most common type of pallet racking, allowing for the direct access to each pallet. It's versatile but may not be the most space-efficient.
- Drive-In/Drive-Thru racking: Designed for high-density storage, these systems allow forklifts to drive directly into the rack. They're great for bulk storage but less so for fast-moving goods.
- Cantilever racking: Ideal for long, bulky items like lumber or pipes. The design allows for easy access but requires specialized handling equipment.
- Automated Storage and Retrieval Systems (AS/RS): These are computer-controlled systems that automatically place and retrieve items. They're highly efficient but come with a high initial cost.
Before investing in any storage system, assess your needs regarding space, types of goods, and retrieval frequency. Choose systems that can be easily adjusted or expanded as your needs change.
Order fulfillment
Order fulfillment is where the rubber meets the road in warehouse logistics. It's the final step of your supply chain that ensures the customer receives what they ordered in the condition they expect and within the time frame promised.
It is more than just a logistical necessity; it's a competitive advantage and a key touchpoint in the customer experience. Errors or delays here can lead to customer dissatisfaction, negative reviews, and even lost business. Conversely, a smooth and speedy fulfillment process can boost customer loyalty and give you a competitive edge.
Here are the steps involved when fulfilling orders:
- Order receipt: The process starts when an order is received, either manually or through an integrated system like a Warehouse Management System (WMS).
- Picking: Workers retrieve the ordered items from their storage locations. This step needs to be quick but also error-free.
- Packing: Items are then packed securely to prevent damage during shipping. This often involves choosing the right type of packaging material and method.
- Shipping: Finally, the packed items are loaded onto a truck for delivery to the customer.
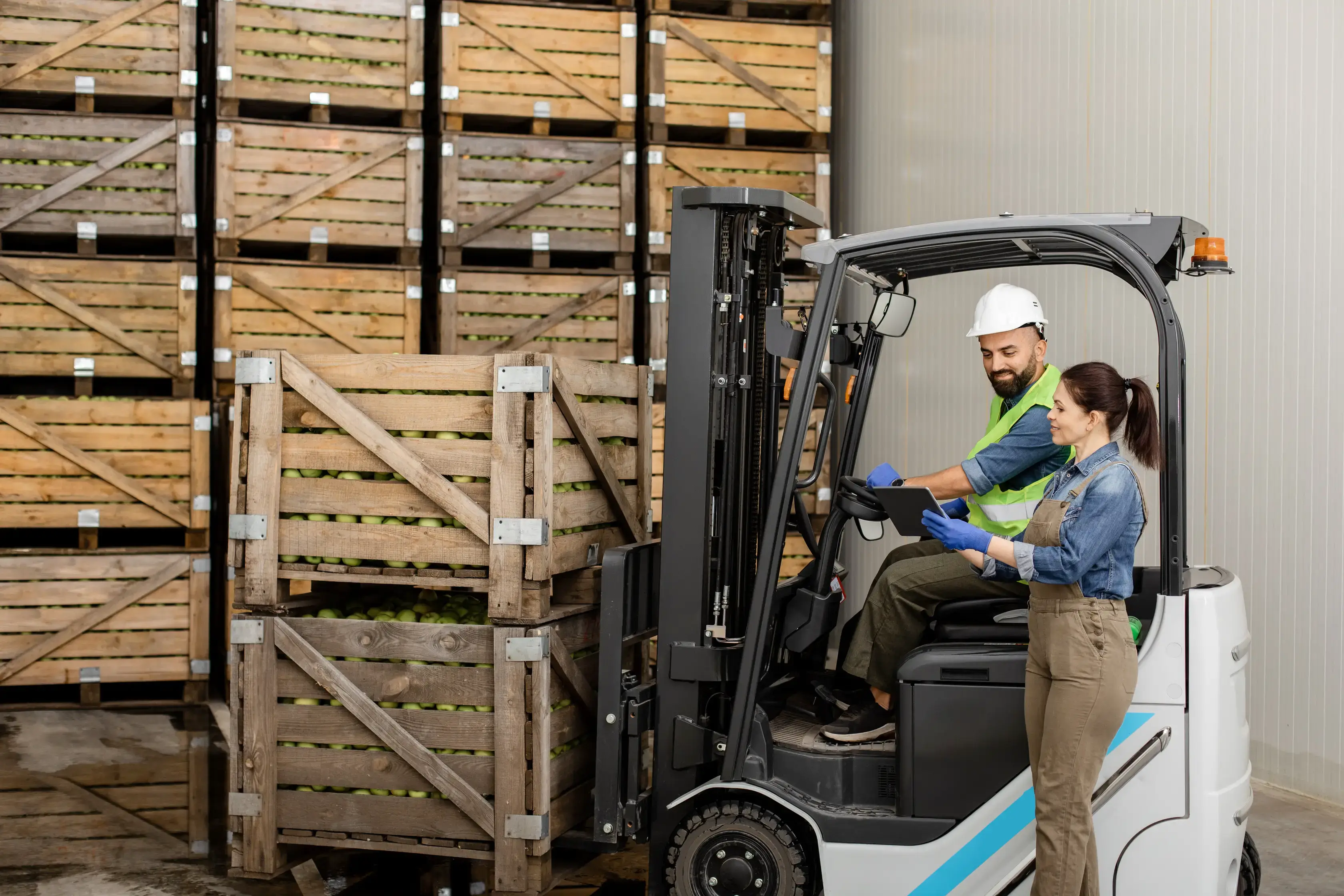
A WMS can automate many processes between these steps, reducing the chance of human error. Handheld scanners can speed up the picking process, and automated packing machines can ensure consistent and secure packaging.
Offer customers real-time tracking of their orders. This not only enhances the customer experience but also allows you to monitor the efficiency of your shipping process.
Warehouse layout design
The layout of your warehouse is like the foundation of a building; it streamlines operations, improves inventory control, and can significantly reduce costs. So, if it's not solid, everything built on top of it is compromised.
A poorly designed layout can create bottlenecks in your warehouse operations, increase retrieval times, and even pose safety risks.
Designing the layout of your warehouse isn't a one-off task; it's an ongoing process that should adapt to the evolving needs of your supply chain. Here are some key factors to consider:
- Flow: The layout should facilitate a logical flow of goods from receiving to storage to shipping. This minimizes handling and movement, saving both time and labor costs.
- Accessibility: All items should be easily accessible to reduce retrieval times. This is particularly important for high-turnover items.
- Space utilization: Maximize vertical space to get the most out of your warehouse footprint. This often involves choosing the right storage systems.
- Safety: Ensure that the layout adheres to safety regulations, including clear aisles and emergency exits.
Use data on your inventory turnover, sales trends, and seasonal fluctuations to inform your layout design. Your warehouse staff are the ones on the ground, so involve them in the planning process. They can provide valuable insights into what works and what doesn't.
Challenges in warehouse logistics and practical solutions
Even with the best-laid plans and most advanced technology, challenges in warehouse logistics are inevitable. These hurdles can range from everyday issues like space utilization to more complex problems like data management.
Space Utilization
As your business grows, so does your need for warehouse space. However, expanding a warehouse or moving to a larger facility is costly and disruptive. Optimize your storage systems instead. High-density storage systems like drive-in racking can significantly increase your storage capacity without requiring more floor space.
If you can't expand outward, consider using taller storage units and equipment capable of reaching higher levels.
Labor Costs
Skilled labor is essential for efficient warehouse operations, but it also represents one of the largest operational costs.
Warehouse automation can help your logistics operations, especially in repetitive tasks that require efficiency around the clock. Also, train workers in multiple roles to ensure flexibility and reduce downtime due to absences or turnover.
Data Management
With so many moving parts, keeping track of everything—from inventory levels to order statuses—can be overwhelming.
Use a Warehouse Management System (WMS) that integrates with other business systems like your inventory management system, ERP, and CRM to centralize data. Also, implement technologies like RFID and IoT sensors for real-time inventory data, equipment status, and more.
Regulatory Compliance
Warehouses must also adhere to various regulations, from occupational safety standards to environmental guidelines. These regulations can change, so it's crucial to stay updated and adjust your operations accordingly.
Conduct regular internal audits to ensure compliance and identify areas for improvement.
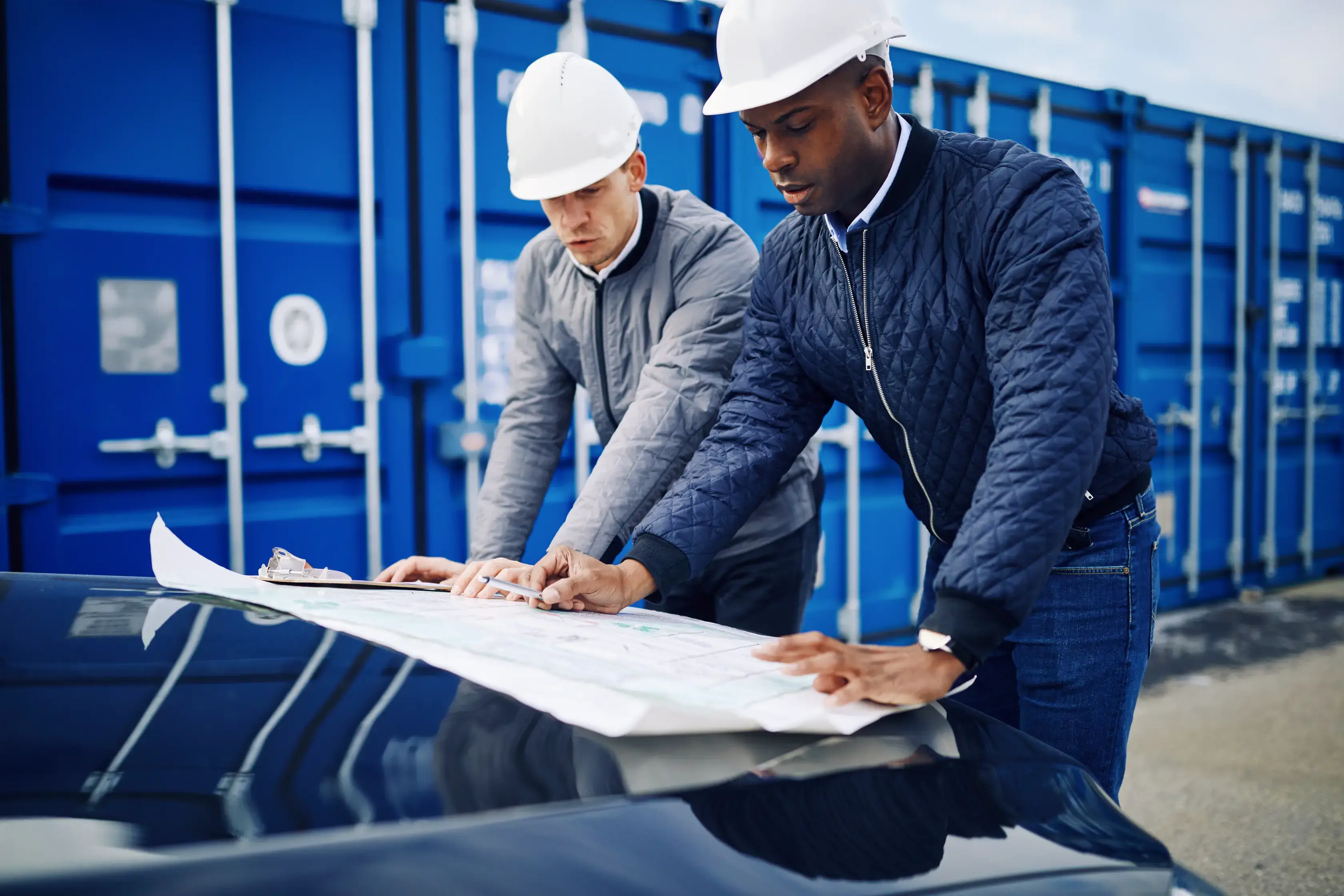
Tips for optimized warehousing logistics
Getting your warehouse logistics right is very important for efficient supply chain management. Here's how to optimize your warehousing logistics system:
1. Ensure your warehouse goals align with your broader supply chain objectives. Regularly review key performance indicators (KPIs) like order accuracy, fulfillment speed, and inventory turnover in the context of your overall supply chain goals. Use these metrics to adjust your warehouse operations as needed.
2. Streamline inbound and outbound flows to efficiently manage the movement of goods into and out of the warehouse. For inbound flows, coordinate with suppliers to schedule delivery times during off-peak hours. Use a dock scheduling system to manage these time slots effectively and avoid truck queues.
For outbound flows, use a time slot management system to prioritize orders based on shipping schedules and carrier arrival times.
Discover how Kompak Nederland, a leader in the European FMCG industry, optimized its warehouse logistics using GoRamp's Time Slot Management System.
3. Implement real-time tracking. Utilize technologies like RFID tags and IoT sensors that feed real-time data into your WMS. This allows for immediate adjustments in case of discrepancies like customer returns and enhances visibility across the supply chain.
4. Adopt Just-In-Time (JIT) inventory. Use a management software that gives you access to real-time data on inventory levels and order statuses. Use demand forecasting tools to predict your inventory needs closely. Coordinate with suppliers for more frequent, smaller deliveries to maintain low inventory levels while meeting demand.
5. Enhance worker training. A well-trained workforce can adapt to new technologies and procedures more quickly. Regularly update training programs to include the latest best practices and technologies. Consider implementing a Learning Management System (LMS) to track employee progress and identify areas for further training.
Leveraging GoRamp’s logistics solutions for efficient supply chain management
GoRamp offers a suite of software solutions designed to streamline various aspects of warehouse and supply chain management. From dock scheduling to queue management, GoRamp's software solutions can be a valuable addition to your workflow.
GoRamp's Dock Scheduling Tool helps manage the arrival and departure of trucks at your warehouse docks. It allows suppliers and transportation providers to book specific time slots for loading and unloading. This minimizes congestion at the docks and ensures a smoother flow of goods into and out of the warehouse.
GoRamp's WMS also helps you automate key warehouse processes like inventory tracking, order processing, and labor management.
The integration with other GoRamp tools ensures that data flows smoothly across all systems, providing a unified view of your operations. Book a demo to see all the logistics solutions at GoRamp.