A supply chain manager's job in a warehouse is one of the most responsible. Primarily because the smoothness and productivity of manufacturing and retail businesses are dependent on the timely supply. If the pallets of production do not arrive on schedule, or if their arrival time is not foreseen, the manufacturing processes halt, as does the product distribution to the customers.
The challenging situation in the logistics sector, along with market uncertainties, is causing even more stress and chaos for the day-to-day work of supply managers. It is more critical than ever to have an effective Warehouse management system for clear planning and tracking of supply delivery.
So, how can your work and procedures be organized more adequately? There are smart solutions to the problem, for example, work with an efficient online Dock scheduling system, but first, let’s map the main problems to solve.
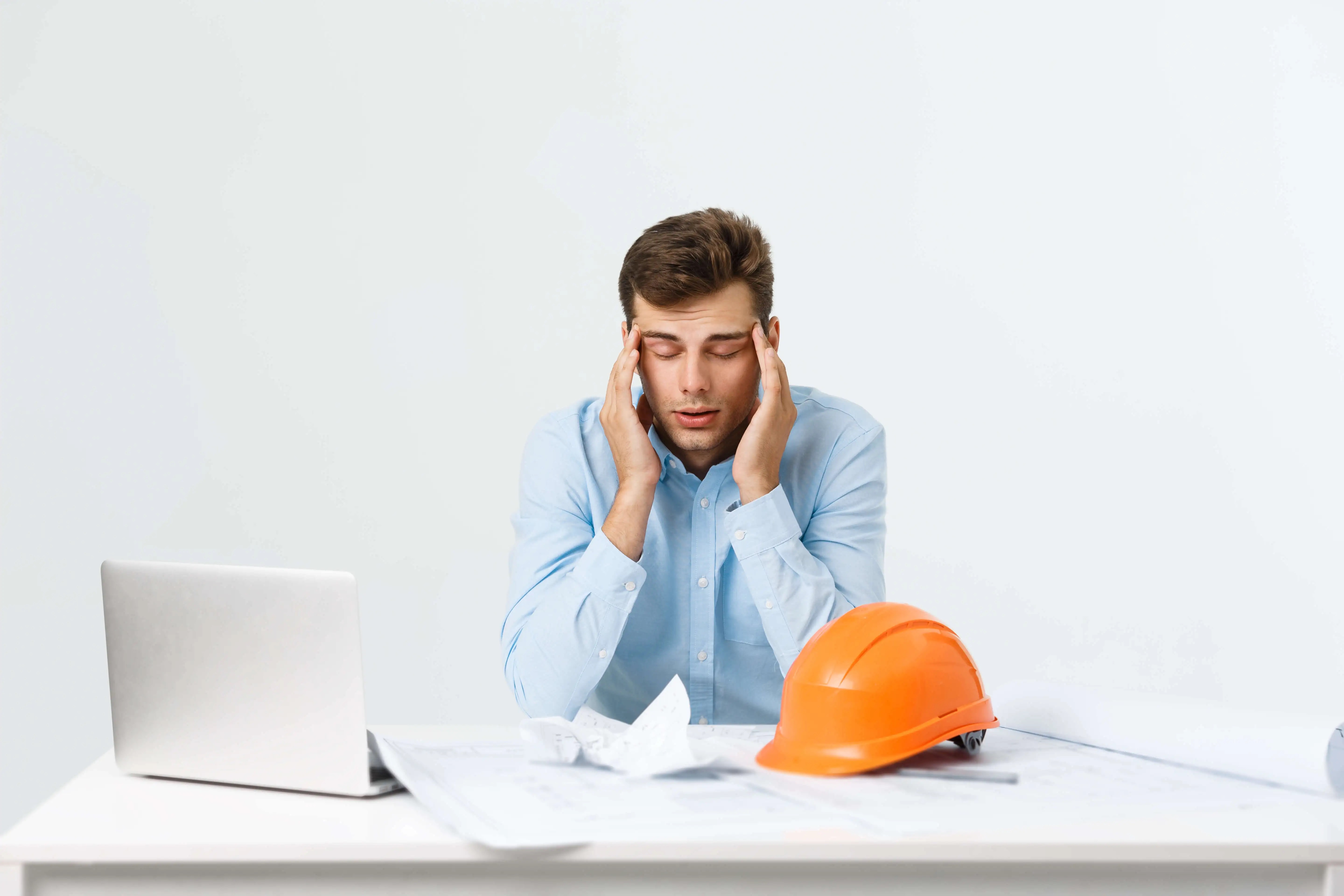
External Disruptions
Of course, the pandemics transformed the way the supply chain works. Safety measures and restrictions have changed everything. Closing entire cities and ports for a few weeks, thus stopping supply chains, on a day's notice has become the new normal.
The global labour shortage is also not making things easier. The ongoing driver shortage is increasing transportation costs and delivery times. More countries are starting to have a hard time filling open positions in the warehousing and manufacturing sectors. Finding people to work with is becoming a real challenge.
Rising raw material, energy and fuel prices are making production planning a real headache. With prices reaching new heights and constantly changing, you can only guess what your supply costs will look like in 6 months.
These processes make foreseen planning and clear online visibility of the supply arrivals even more important.
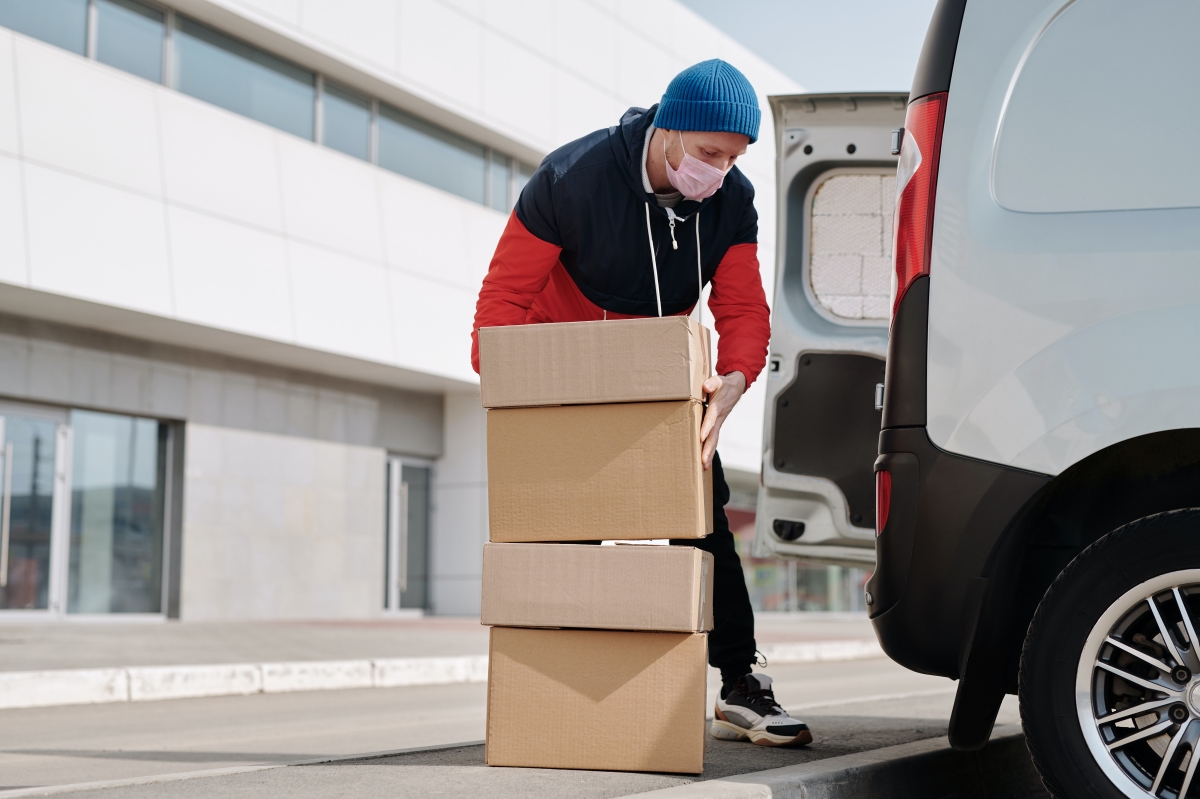
Internal Challenges
On the other hand, we have list of pains rising from within the organization. The most common issue is not knowing when the raw materials will arrive. Often, inbound truck arrival times, truck plate numbers or delivery delay information is not reaching the supply chain manager on time. It is a piece of critical information to the entire production and end-product delivery process. Efficient production and supply chain management is based on planning and with missing information, it is impossible to create feasible plans.
Check out GoRamp's Gate Management feature and eliminate mistakes in communication & dependency on warehouse gatekeepers.
Often, manual communication and messy information exchange results in inconsistent processes and errors. Collecting, checking and re-sending delivery information via phone or emails is slow, time-consuming and if mismanaged, it can be chaotic. At the same time, everything is in the hands of a few employees that can easily become a bottleneck for the supply and production processes.
If you do not have a clear warehouse management system, most likely you do not have a systematic overview of the warehouse capacity and workload, and that is another struggle for supply chain managers. All planning and coordination efforts to get the raw materials on time will fail if your warehouse docks are jammed. On top of that, the waiting trucks will start counting penalties for truck detention.
Mor Furniture, American furniture retailer, shared how GoRamp improved business operations:
"As a furniture retailer with multiple distribution centers, we needed software that would help manage our warehouse docks. Using the GoRamp system we have a system that allows carries to self serve to schedule appointments in addition to capturing metrics which will allow us to track carrier and warehouse performance. The reservations calendar allows key users to monitor warehouse activity across the entire chain. The UX of the GoRamp platform was intuitive which allows us to onboard warehouse personnel and carriers quickly."
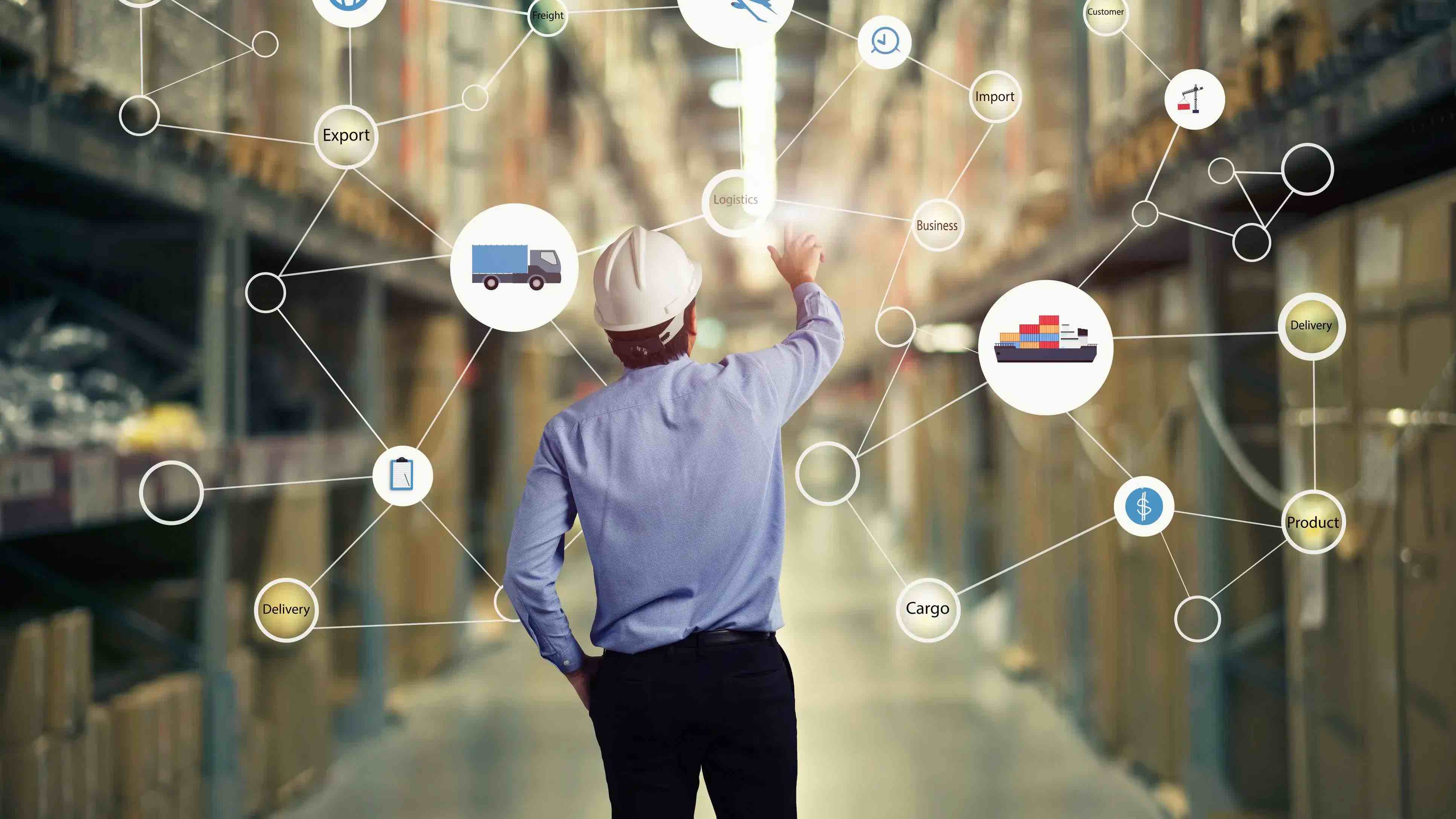
How a Dock Management System can Fix This?
External pain points are something that is completely out of supply chain managers' hands. Still a good supply chain manager must manage the risks and prepare for the upcoming uncertainties. The ability to plan supply arrivals in advance is a crucial factor for efficient and effective work even in difficult times. So, a clear view of the inbound truck flow, as well as fast and clear information exchange between logistics, warehouse colleagues, carriers, and drivers, make even worst external situations more predictable and manageable.
Internal challenges also require tools to increase predictability. A proven way to solve the lack of communication and information exchange is to fully automate the warehouse dock scheduling process. There are plenty of unified designed Warehouse scheduling softwares and Dock management system tools that are handy, convenient, and reasonably priced.
Working with Time Slot management system and transferring time slot booking from phone calls and emails to a dock scheduling platform will improve visibility and streamline the inbound truck management process.

How can You Improve Logistics Processes with the Dock Scheduling Software?
Dock scheduling systems help plan occupancy of loading platforms in advance and optimize operations at the warehouse. The solution also reduces truck downtime and eliminates chaotic truck clutter and unnecessary movement in the warehouse. One of the most important values in the long term is centralized information, which allows complete traceability and the development of efficiency plans. More information you can find in our blog "What is Dock Scheduling?"
Without Dock scheduling software:
- No visibility of inbound
- Trucks congestion
- Random and unplanned arrivals
With Docks scheduling software:
- Reduced driver waiting times up to 40% by planning in advance
- Increased warehouse load capacity by up to 20%
- Clearly scheduled warehouse frees up human & facility resources allowing for extra loading/unloading capacities
- Increased warehouse loading efficiency by 20%
- More control & improved planning
Let us show you how a good Dock scheduling tool can solve these pain points.
Book a free 20 min call with our expert to get started!