Key Takeaways
- Manufacturing Warehouse Management Software (WMS) enhances operational efficiency through real-time inventory visibility, process optimization, and integration with ERP systems.
- Key features of WMS include real-time inventory tracking, ERP integration, and quality control, which streamline warehouse operations and improve customer satisfaction.
- Choosing the right WMS involves assessing logistics requirements, vendor reputation, and total cost of ownership to ensure the system meets evolving business needs.
Overview of Manufacturing Warehouse Management Software
Warehouse Management Systems (WMS) are sophisticated software solutions designed to handle and control daily warehouse operations with the utmost efficiency. WMS optimizes warehouse operations by improving processes such as receiving, storage, picking, packing, and shipping. This maximizes labor efficiency, space utilization, and resource allocation. Imagine a well-oiled machine where every cog fits perfectly; that’s what a WMS does for your warehouse.
One of the standout features of WMS is real-time inventory visibility. This means you can track stock levels, inventory movements, and ensure accuracy at all times, which is crucial for effective warehouse management. Real-time data not only helps in managing day-to-day operations but also supports strategic decision-making by providing insights into inventory trends and demands. This visibility is a game-changer, allowing businesses to respond promptly to market changes and customer needs.
Moreover, the integration of WMS with ERP systems takes warehouse management to the next level. Seamless data sharing between WMS and ERP systems enhances production planning and order fulfillment. This integration ensures that every aspect of the supply chain is synchronized, from raw material procurement to final product delivery, thereby minimizing delays and maximizing efficiency. In a world where time is money, such integration is invaluable.
Key Features of Manufacturing Warehouse Management Software
The backbone of any robust WMS lies in its powerful features. These features collectively improve operational efficiency by monitoring and optimizing processes at various levels. From receiving and storage to picking, packing, and shipping, WMS supports these critical activities to ensure smooth warehouse operations. Companies like Blue Yonder claim their WMS provides 100% inventory visibility and accuracy while significantly increasing throughput and reducing costs. This is a testament to the transformative power of WMS.
To delve deeper, the key features of WMS can be categorized into three main areas: Real-time Inventory Tracking, Integration with ERP Systems, and Quality Control and Traceability. Each of these features plays a crucial role in streamlining warehouse operations and ensuring that businesses can meet market demands efficiently.
Real-time Inventory Tracking
Real-time inventory tracking is a cornerstone of modern warehouse management systems. With technologies like RFID, WMS can provide accurate and up-to-date information about inventory levels. This capability allows for optimal inventory placement and reduces warehousing costs by optimizing storage, retrieval, and packing processes. Imagine being able to track every item in your warehouse with pinpoint accuracy; the benefits are immense.
Moreover, order picking, which represents approximately 55% of total warehousing costs, is significantly improved through real-time tracking. Ensuring accurate and efficient item picking, WMS reduces errors and speeds up order fulfillment. This not only enhances customer satisfaction but also boosts overall warehouse productivity.
Integration with ERP Systems
Seamless integration between WMS and an ERP system is vital for real-time decision-making and operational efficiency. This integration facilitates better data sharing, allowing for informed decision-making across various business functions. Integrating WMS with other systems allows companies to plan and schedule their operations effectively, ensuring a harmonious supply chain.
Integrated WMS solutions provide a comprehensive view of operations by combining warehouse management with other enterprise resource planning functions. This holistic view is crucial for businesses looking to optimize their supply chain and improve overall efficiency. In a competitive market, having such an integrated system can be a significant advantage.
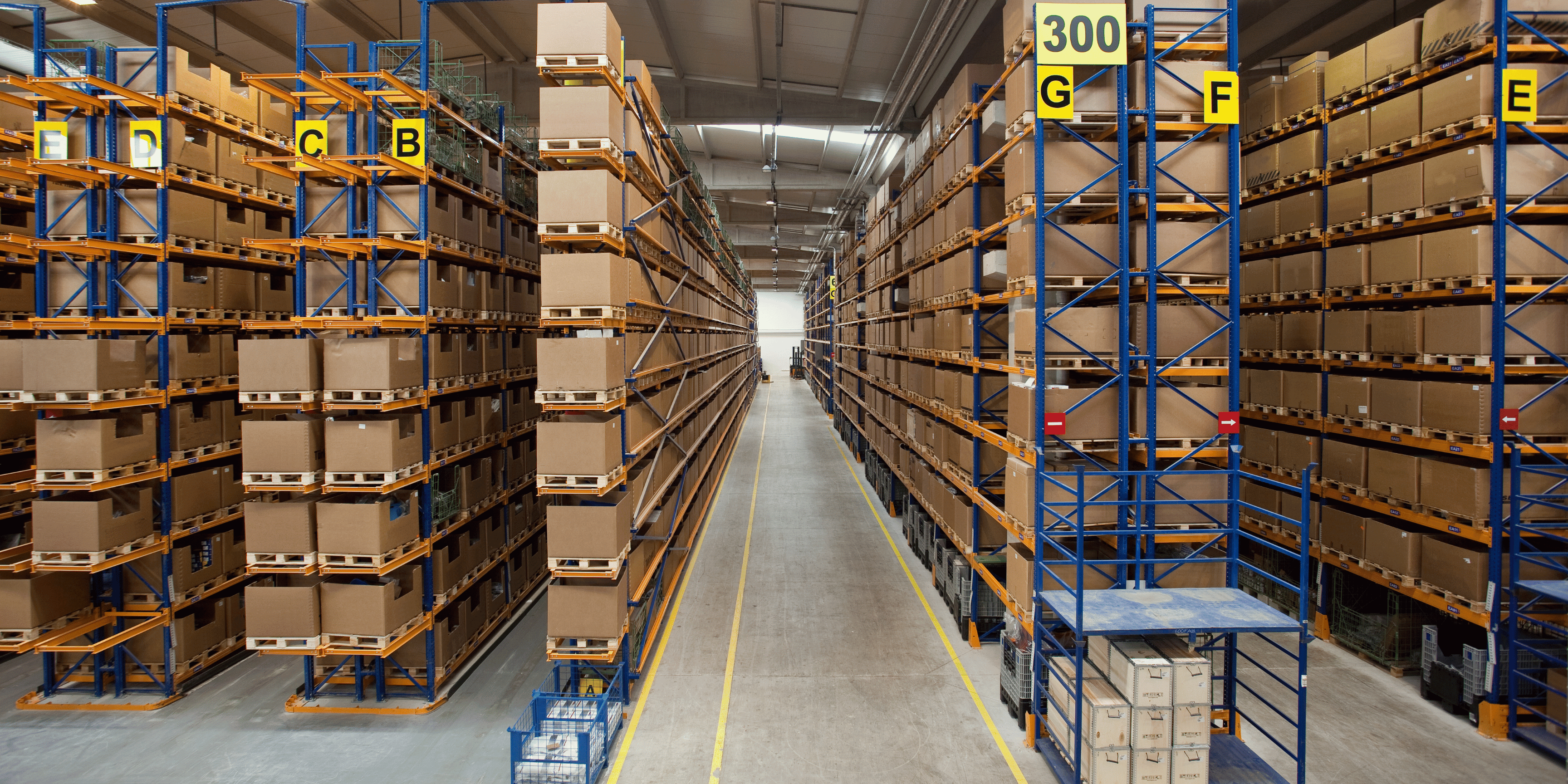
Quality Control and Traceability
Quality control and traceability are critical aspects of manufacturing, and WMS plays a crucial role in these areas. Manufacturers rely on lot tracking capabilities in WMS to manage quality control and swiftly address potential product recalls. This ensures that any issues are quickly identified and resolved, maintaining product safety and compliance with industry regulations.
WMS provides real-time data that enhances the traceability of raw materials and finished products. Effective lot tracking helps manufacturers comply with industry regulations and quickly respond to any safety concerns. This not only protects the brand’s reputation but also ensures customer safety and satisfaction.
Enhancing Production Efficiency
One of the most compelling benefits of WMS is its ability to enhance production efficiency. Automating processes from receiving to shipping, WMS enhances operational efficiency and reduces errors. Imagine a warehouse where every process is streamlined and optimized; that’s the power of WMS. Smart warehouses, equipped with advanced technologies, significantly boost productivity and accuracy.
Effective WMS solutions must address unique challenges faced in manufacturing, such as reverse logistics and efficient handling of raw materials. By doing so, they ensure that every aspect of the manufactured warehouse operation is optimized for maximum efficiency, providing a comprehensive solution.
In this section, we will explore how WMS streamlines logistics processes, incorporates automation and robotics, and optimizes order picking and fulfillment.
Streamlined Logistics Processes
Real-time visibility into inventory across locations enhances operational decisions and speeds up logistics software. With real-time tracking features, companies can monitor the timely arrival of packages and their correct destinations. This increased visibility and control translate to regular updates, real-time communication, and performance feedback for associates, ensuring that every part of the logistics process is running smoothly.
Automation eliminates guesswork and bottlenecks, leading to smoother logistics processes. Supporting planning and scheduling through direct integration with other systems, WMS enhances logistical coordination. This results in increased efficiency, scalability, and reduced human errors in logistics operations.
Predictive maintenance powered by AI also helps in anticipating equipment failures, reducing downtime and maintenance expenses.
Automation and Robotics
Automation and robotics play a crucial role in modern warehouses. Common types of warehouse robots include automated guided vehicles (AGVs) and autonomous mobile robots (AMRs). These robots streamline various processes such as data collection, barcoding, scanning, picking and packing, shipping, and inventory tracking.
The integration of IoT in warehouses significantly boosts automation, helping reduce reliance on human labor and enhance efficiency. Using robots increases operational speed and minimizes human errors, improving overall efficiency. This not only reduces costs but also ensures that warehouses can meet the demands of a dynamic market.
Optimized Order Picking and Fulfillment
Order picking represents a significant portion of warehousing costs, accounting for 55% of the total. WMS guides efficient storage, retrieval, and packing, helping to reduce these costs. Cloud-based WMS offers real-time visibility, scalability, and improved market responsiveness, making it easier to handle speed and agility during peak seasons and adapt to changing market demands.
Optimized order picking and fulfillment ensure that customers receive their manufacturing orders accurately and on time. This not only boosts customer satisfaction but also enhances the overall increased operational efficiency of warehouse operations, especially in light of changing customer buying patterns and changing market conditions. In a competitive market, such sales purchasing efficiency and verification can be a significant differentiator.
Advanced Technologies in Manufacturing WMS
Advanced technologies are transforming the landscape of manufacturing WMS. Key smart warehousing technologies include AI, machine learning, and autonomous robots. These technologies enable manufacturers to respond quickly to market changes and enhance service delivery. Adopting smart warehousing technologies significantly improves operational efficiency and customer satisfaction.
In this section, we will explore how AI and machine learning, IoT integration, and mobile-enabled solutions are shaping the future of WMS. These technologies not only enhance the functionality of WMS but also ensure that warehouses can meet the demands of a rapidly changing market.
AI and Machine Learning
AI and machine learning are crucial technologies that guide the decision-making of warehouse robots. By analyzing IoT data, AI provides predictions and insights that enhance decision-making and operational efficiency. This dynamic response to changes is vital for effective warehouse management.
Real-time dashboards and analytics are also essential for effective management and performance monitoring in a WMS. These tools provide valuable insights and help in making informed decisions that enhance overall efficiency and productivity.
Internet of Things (IoT) Integration
IoT devices facilitate real-time inventory control by sending data through various tools like smartphones and RFID. Data sources such as sensors, conveyors, smartphones, handheld devices, radio beacons, and RFID significantly contribute to the IoT capabilities in warehouse management. This seamless integration enhances the functionality and efficiency of WMS.
By integrating IoT devices into WMS, companies can achieve real-time data and seamless integration. This not only improves inventory tracking but also ensures that warehouses can respond promptly to market changes and customer demands.
Mobile Enabled Solutions
Mobile devices facilitate real-time inventory management, enabling quick data access and updates. These devices also support real-time communication between workers, improving on-the-go inventory management. By using mobile technology, warehouse staff can manage inventory and receive updates while moving throughout the facility, ensuring that inventory is effectively managed.
Mobile-enabled solutions ensure that multiple warehouses can operate efficiently and respond quickly to market demands. This not only improves overall efficiency but also enhances customer satisfaction by ensuring timely and accurate order fulfillment.
.png)
Types of Manufacturing Warehouse Management Systems
Understanding the different types of WMS is crucial for making the right choice for manufacturing operations. Different warehouse management systems are designed to meet varying operational needs, making it essential to understand their specific advantages and limitations. In this section, we will explore standalone WMS, cloud-based WMS, and integrated WMS solutions.
Each type of WMS has its unique benefits and limitations. Standalone WMS offers extensive features specifically tailored for warehouse operations but may require substantial investment and maintenance. Cloud-based systems provide flexibility and lower up-front costs compared to standalone WMS. Integrated WMS solutions offer a holistic view of the business by combining warehouse management with other enterprise resource planning functions. For more information on types of WMS, refer to the comprehensive guide on the GoRamp Blog.
Standalone WMS
Standalone warehouse management systems typically offer the most extensive features specifically tailored for warehouse operations. These systems are easier to operate since they focus solely on warehousing tasks, avoiding the complexity of broader supply chain features. However, a major drawback of standalone WMS solutions is their limited access to data outside of warehouse operations, which can hinder decision-making.
In summary, standalone WMS can enhance warehouse efficiency but may limit insights needed for broader operational decisions. It’s important to weigh these pros and cons when considering a standalone WMS for your business.
Cloud-based WMS
A cloud-based warehouse management system leverages cloud technology for robust features and cost-effective implementation. These systems offer scalability, allowing businesses to adapt quickly to market changes. By eliminating various costs associated with hardware and administration, cloud-based WMS systems are more affordable.
Cloud systems ensure quick implementation in weeks and guarantee reliability through cloud server redundancy. This makes them a highly adaptable option for businesses looking to enhance their warehouse operations without significant upfront investment. Additionally, the oracle warehouse management cloud provides further benefits for optimizing these processes, includingsoftware as a service solutions.
Integrated WMS Solutions
Integrated WMS systems are typically part of broader ERP or supply chain management solutions. These integrated systems provide better integration with other solutions, offering a holistic view of the business. This comprehensive approach ensures that all aspects of the supply chain are synchronized and optimized.
Leveraging integrated WMS solutions streamlines operations and improves overall efficiency. These systems offer seamless integration with other enterprise functions, making them ideal for companies looking to optimize their entire supply chain.
Case Studies: Success Stories in Manufacturing WMS
Companies that implement manufacturing warehouse management software can achieve maximized efficiency. For instance, Iceco Group, a leader in real estate and food production distribution, overcame significant logistics challenges and experienced a 25% reduction in operational costs after adopting GoRamp's WMS. This significant improvement highlights the transformative power of WMS in enhancing inventory management.
Another success story is Arctic Logistics, which enhanced picking accuracy and streamlined shipping processes after switching to a new WMS designed for their 3PL operations. These examples demonstrate the real-world benefits of implementing WMS and how it can lead to substantial improvements in warehouse operations.
Choosing the Right Manufacturing WMS for Your Business
When selecting a warehouse management system, it is crucial to consider the specific logistics requirements of your business, including how it handles order types and inventory management. It’s important to choose a WMS that is flexible and can adapt to changing business needs and processes over time. Evaluating the reputation and stability of the WMS vendor is also key to ensuring long-term support and reliability.
Understanding the pricing model and total cost of ownership for the WMS, including implementation and maintenance, is critical for budgeting. Considering these factors helps businesses make an informed decision and select a WMS that aligns with their operational needs and budget constraints.
Summary
In summary, manufacturing warehouse management software offers a multitude of benefits that can transform warehouse operations. From real-time inventory tracking and ERP integration to quality control and advanced technologies like AI and IoT, WMS enhances efficiency, accuracy, and responsiveness. The right WMS can streamline logistics processes, incorporate automation and robotics, and optimize order picking and fulfillment, ultimately leading to improved productivity and customer satisfaction.
As businesses navigate the complexities of modern supply chains, implementing a robust WMS can be a game-changer. By choosing the right WMS that aligns with their specific needs and budget, companies can achieve significant improvements in operational efficiency and maintain a competitive edge in the market. The journey to warehouse excellence begins with the right WMS.
Frequently Asked Questions
What is a Warehouse Management System (WMS)?
A Warehouse Management System (WMS) is essential software that controls and optimizes daily warehouse operations, including receiving, storage, picking, packing, and shipping. Implementing a WMS can significantly enhance operational efficiency in your warehouse.
How does WMS improve inventory management?
WMS significantly enhances inventory management by offering real-time visibility into inventory levels, which enables optimal stock management and minimizes warehousing costs through the optimization of storage, retrieval, and packing processes.
Why is integration with ERP systems important in WMS?
Integration with ERP systems is crucial in WMS as it facilitates seamless data sharing, enhances production planning and order fulfillment, and offers a comprehensive overview of operations. This synergy leads to improved efficiency and decision-making.
What are the benefits of using automation and robotics in warehouses?
Utilizing automation and robotics in warehouses significantly minimizes human errors and enhances operational efficiency. This leads to streamlined processes in data collection, inventory tracking, and other critical warehouse functions.
How do I choose the right WMS for my business?
To choose the right WMS for your business, evaluate your logistics requirements, flexibility, vendor reputation, and total cost of ownership, ensuring it aligns with your operational needs and budget. Making informed choices in these areas will lead to a successful implementation and long-term satisfaction.