The more efficient your processes are, the more productive the warehouse staff is. This, in the end, leads to better performance and better results. There are also some tools to help you improve warehouse efficiency such as Warehouse management system.
However, this is easier said than done. Finding productivity killers takes time, it requires research, experimenting and some sort of change. Meanwhile, you still need to carry out your daily tasks and keep your whole operation running.
Fortunately, we have analysed many warehouse and distribution center operations throughout the world, and identified the most common efficiency killers in warehouses.
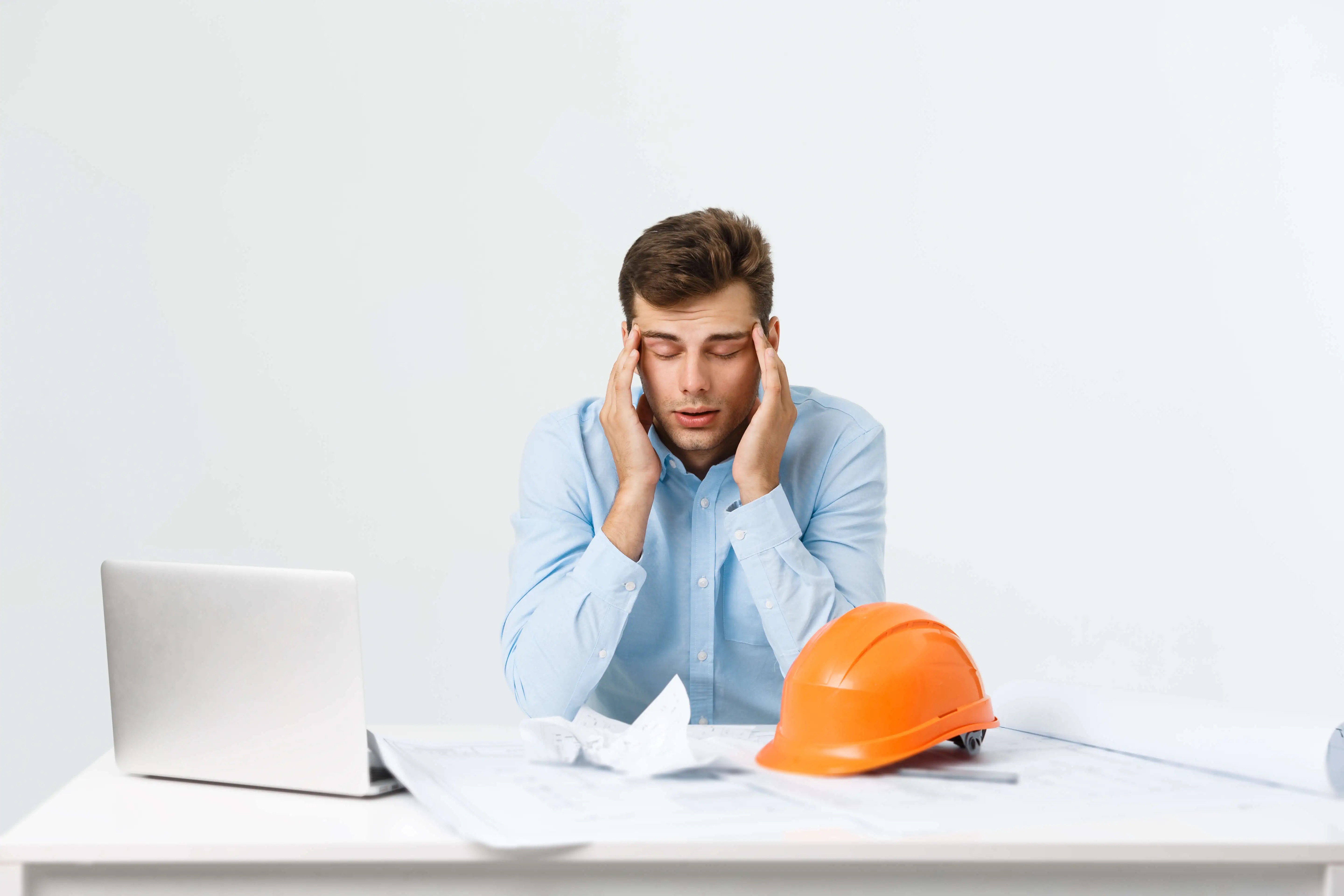
Using the Wrong Tools
It is very common and natural to stick to the tools and techniques that worked for you in the past. And it perfectly makes sense, as long as you don’t stop looking for new and better ways. But most people tend to stop looking for better tools and keep applying the same old techniques for everything. As the saying goes, if you have a hammer, then everything is a nail.
In the warehouse context, this can be often seen in the dock booking process. Most people use excel spreadsheets to log incoming and outgoing truck details, arrival times and other information. Spreadsheets were an innovative tool for the dock booking process 20 years ago. But is it still today or has it become a silent efficiency killer?
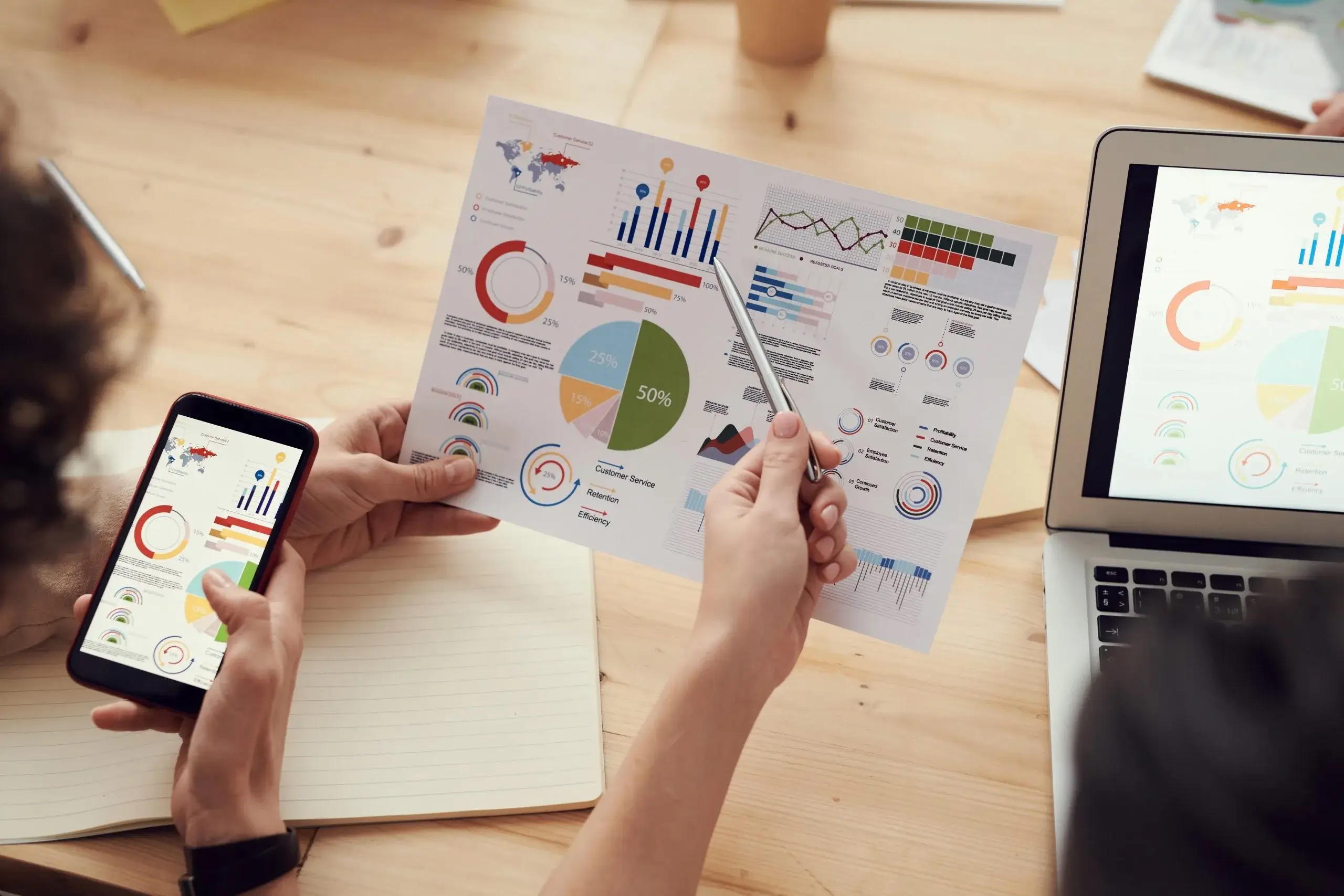
Drowning in Paperwork
It is 2022 and supply chains are still drowning in paperwork. There is an absurd amount of paper that is used in the process of moving and storing goods. For example, truck drivers need to carry nearly 100 pieces of paper for each trip! That is a ton of paper that very easily could be replaced by electronic documents.
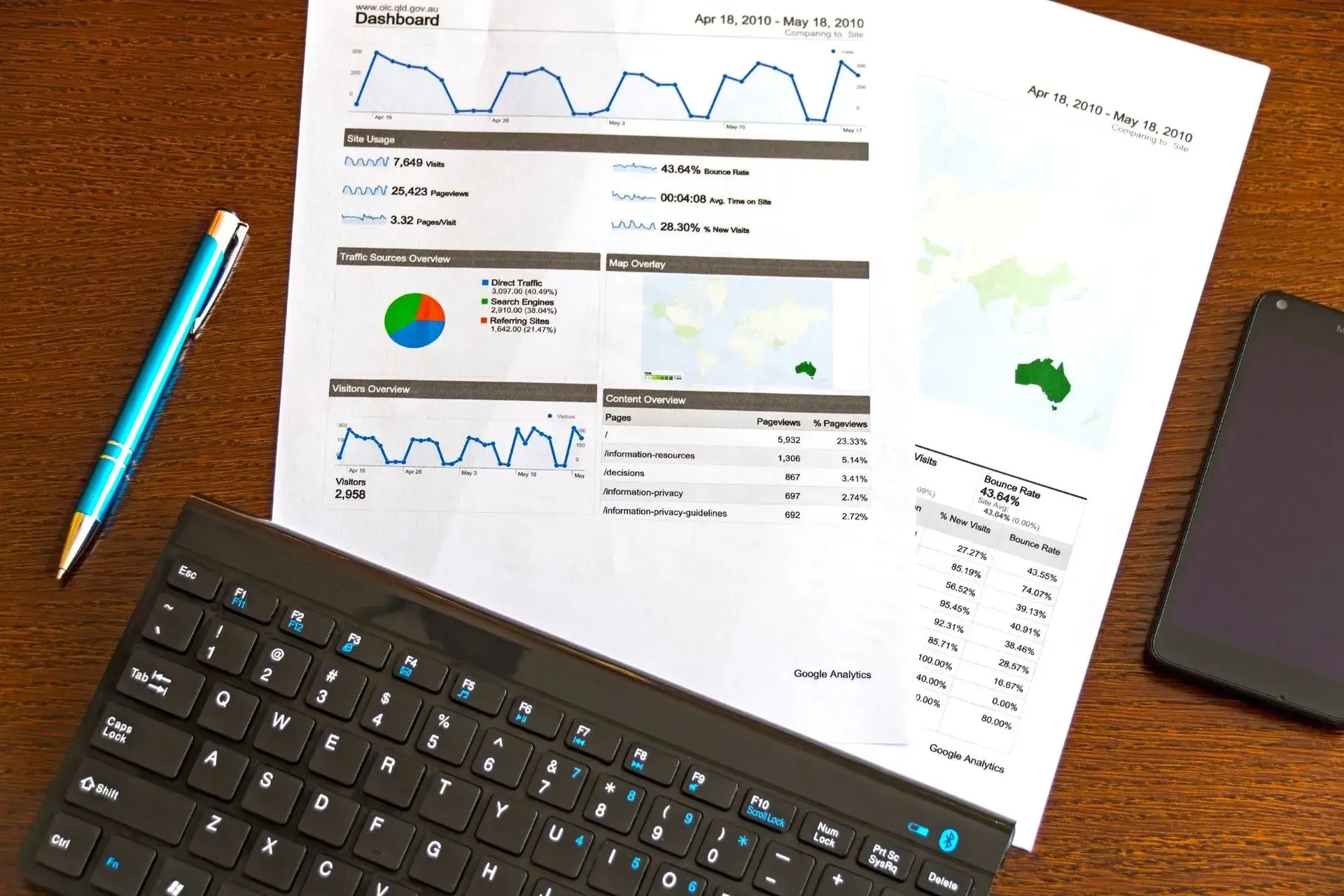
A warehouse is no exception. With all receipts, orders, bills, reports and other records, there is a huge amount of paper that needs to be processed. It needs to be printed, handed over, signed, stored and found when needed. It is a slow and time-consuming process that no one likes to do. When possible, replace paper documents with electronic ones.
Fighting with Truck Congestions
Do you see trucks queuing at your warehouse? Do you get complaints from drivers and carriers about the waiting times at your warehouse? If this is happening in your facility it is a clear sign that your dock scheduling process isn’t working. Poorly working dock scheduling process is a major efficiency killer in every warehouse and distribution centre. Truck detention fines are only one side of the consequences.
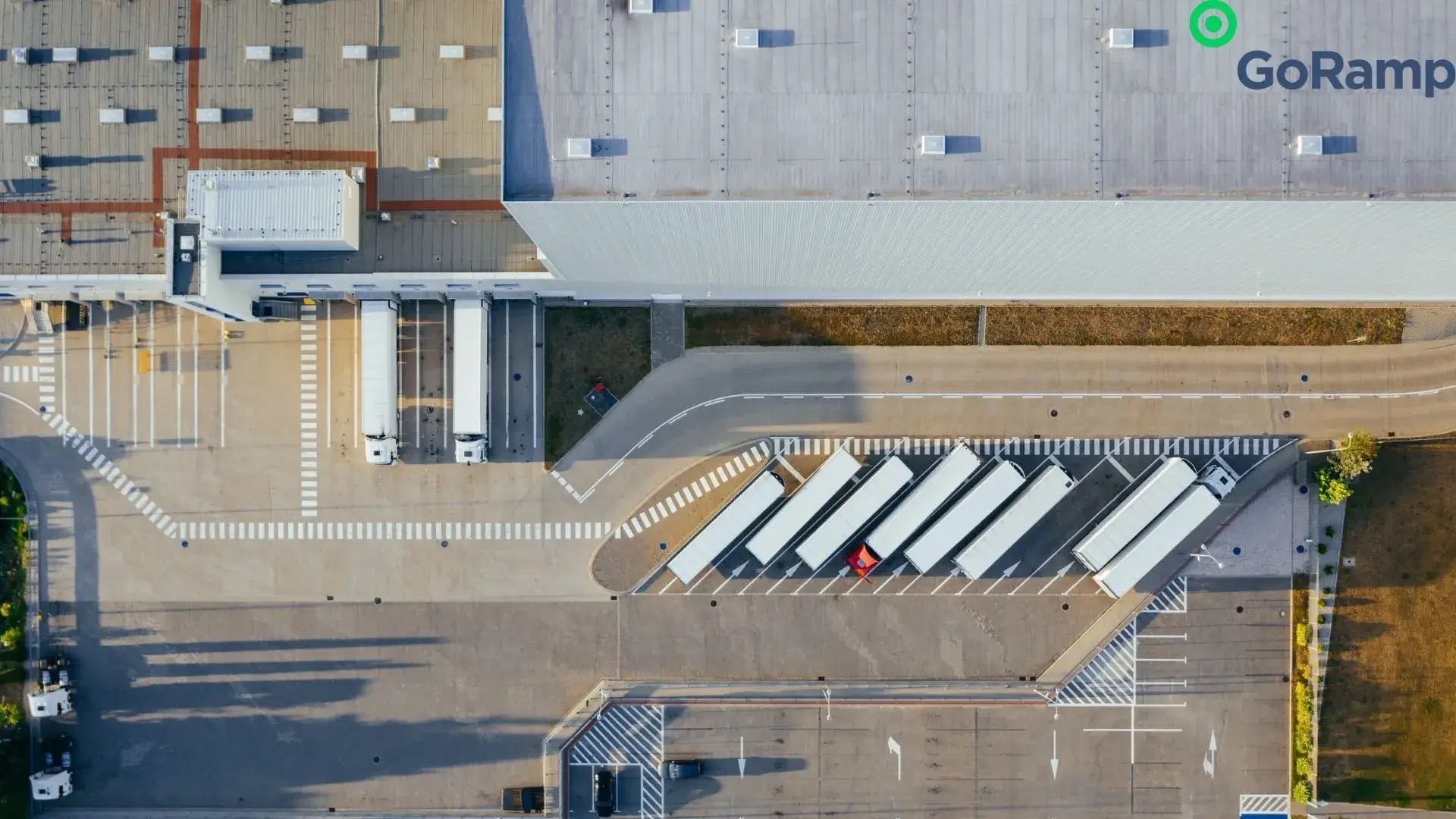
Truck congestions put your whole operation out of sync since you have to start putting out fires one after another. Consider fixing your dock scheduling process as soon as possible. A solution for this problem - Dock scheduling system.
Uneven Workload
It is Monday, 8:00 and you already see 12 trucks lined up, waiting to be loaded. And every Monday is like this. Sound familiar? Recurring peak times are one of the most common efficiency killers. Uneven workload throughout the day is especially harmful to the warehouse staff. People get tired and stressed quickly when they need to process all trucks at once. A good Dock scheduling software helps to distribute workload throughout the whole day.
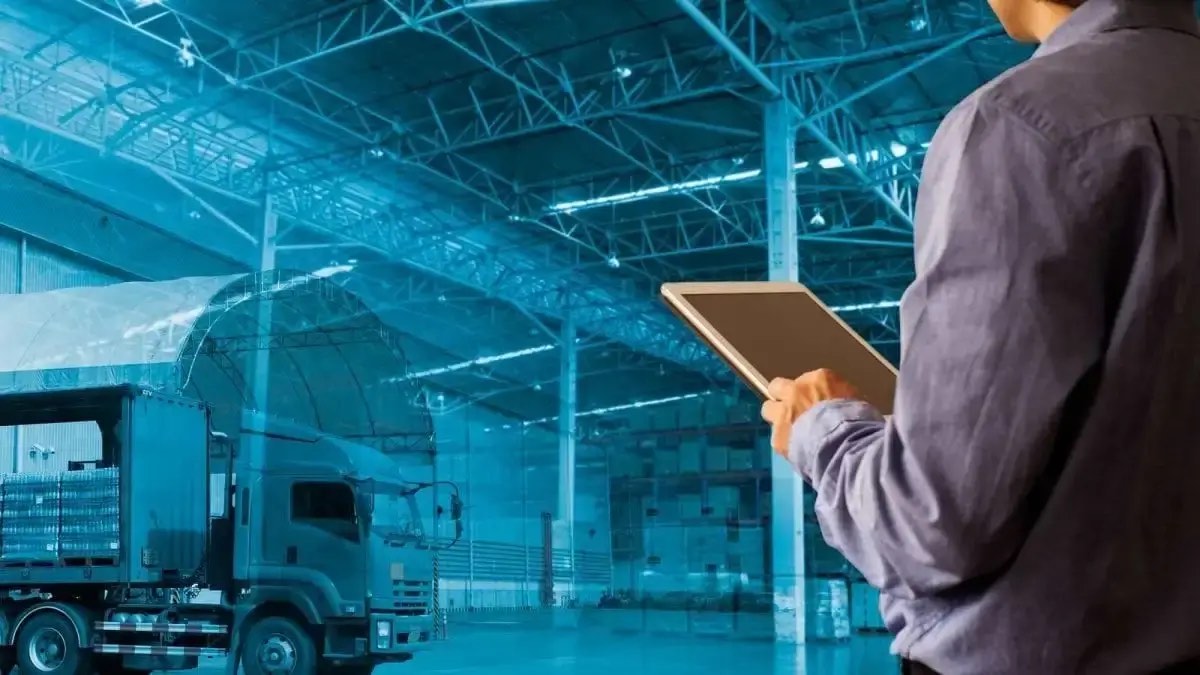
How to Avoid Them
You can easily eliminate these efficiency killers with a Dock scheduling platform. By automating and digitalizing the entire dock booking process, you will get rid of time-consuming repetitive tasks and your team will be able to focus on tasks that matter the most along with our common warehouse problems.
Skretting Canada, a global leader in nutritional solutions for aquaculture, was asked how has GoRamp improved their business operations and what specific benefits they observed since implementing our solution:
"Our Calendar has allowed the whole team to see and plan ahead for the next week. It has put accountability on the carriers to schedule their trucks accordingly and meet their deadlines.Also, full visibility for the warehouse team was improved. It has gave them a schedule to know what trucks are needed and they can pre pick them accordingly."
Sign up for a quick call with our expert to learn more about how we can help you.