Manufacturing is as much about delivering products as it is about creating them. That's why manufacturing logistics is essential. It ensures that materials are on hand for production and that finished goods get to where they need to go.
In this guide, we'll break down the key logistics components within the manufacturing sector and the elements that make up a good logistics strategy. We will also discuss the challenges manufacturers face in logistics with practical ways to solve them.
Defining logistics in a manufacturing context
Logistics is a broad field that covers the planning, implementing, and managing the flow of goods and services. In manufacturing, logistics goes beyond merely shipping products. It involves a series of interconnected processes, including procuring raw materials, coordinating with suppliers, managing inventory, and ensuring that products are delivered to the right place at the right time.
Logistics is often used interchangeably with supply chain, but they're not quite the same. Logistics processes focus on moving and storing goods, ensuring products get from their origin to their destination efficiently. On the other hand, the supply chain encompasses a broader range of activities, from sourcing raw materials to delivering the final product to customers.
Within the manufacturing context, four key components make up logistics:
- Transportation: This deals with moving raw materials to the manufacturing facility and delivering finished products to distributors, retailers, or customers. It's about selecting the best modes of transportation, whether by truck, rail, air, or sea and optimizing routes for cost and speed.
- Warehousing: Once products are manufactured, they need to be stored before they're shipped to their next destination. Warehousing is more than just storing goods. It's about efficiently organizing and tracking them, often facilitated by Warehouse Management Systems (WMS). In some cases, Third-Party Logistics (3PL) providers can take over this function, offering specialized services that can improve efficiency and reduce costs.
- Inventory Management: This is about balancing the stock of raw materials, work-in-progress, and finished goods. Whether raw materials or finished products, knowing what you have, where it is, and how much you'll need can significantly impact your bottom line. Mistakes here can lead to overstock or stockouts, both of which are costly.
- Information Flow: Information is the glue that holds all other components together. Effective communication among various departments, suppliers, and distributors is vital. Today, many companies use Transportation Management Systems (TMS) to streamline information flow and make data-driven decisions.
Elements of a good manufacturing logistics strategy
A high-quality logistics strategy covers everything from production scheduling to transport procurement. But, some important elements must be present for operational efficiency.
Partners and vendors
Choosing the right partners and vendors is one of the most critical elements of your logistics operations. They are responsible for supplying raw materials, storing inventory, or managing your entire warehousing operations if you opt for Third-Party Logistics (3PL) services. So, be careful because this decision can have a long-lasting impact on your manufacturing process.
When vetting potential partners, look beyond transportation costs. Sometimes, it's not just about who offers the lowest price but who provides the best value. Reliability, speed, and quality often outweigh the benefits of a slightly lower cost.
The cheapest option today might not be so cheap if you factor in potential disruptions, delays, or quality issues down the line.
Route planning and optimization
Transporting goods is never as simple as getting from point A to point B. Many factors, like traffic, fuel costs, and delivery windows, come into play.
The importance of route planning extends to both short-haul and long-haul transportation. For short-haul, the challenges often revolve around making multiple stops within a limited geographical area, which requires a detailed plan to minimize time and fuel costs.
Long-haul routes must be optimized for challenges like varying speed limits, toll roads, or international border checks.
There are various transport software with routing management options that consider different variables to suggest the most efficient path. And it's not a set-it-and-forget-it solution; you can adjust to accommodate unforeseen issues like road closures or delays.
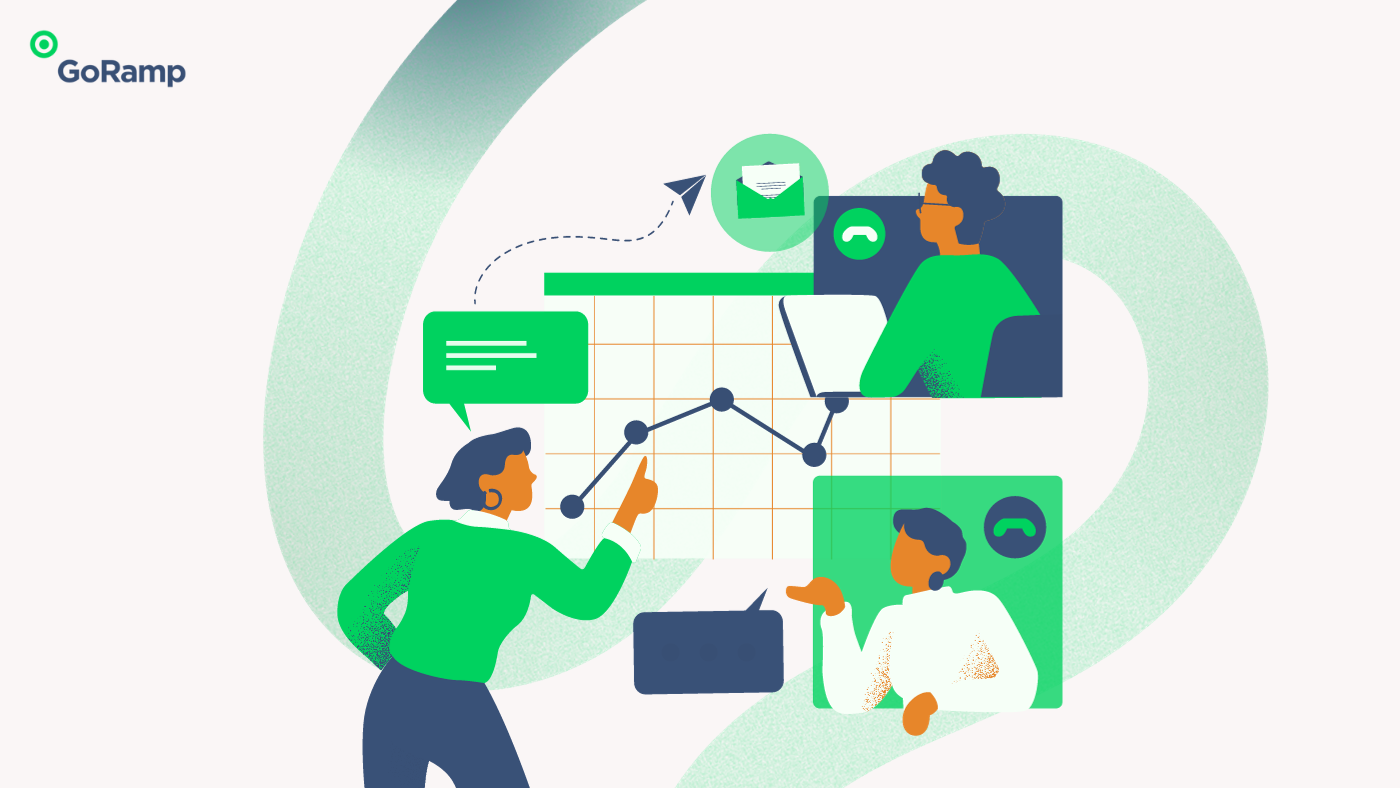
Inventory forecasts and demand planning
These two processes are vital in supply chain management. If you are using a Warehouse Management System (WMS), you can integrate historical sales data, seasonality factors, and even market trends to provide more accurate forecasts.
The idea is to have just the right inventory levels: enough to meet demand but not so much that you're wasting resources on storage and maintenance.
Demand planning goes hand in hand with forecasting. This involves a more detailed approach of looking at specific products or individual SKUs to predict future needs and avoid excess inventory.
With effective dock scheduling software, you can optimize the inflow and outflow of goods in your warehouse, ensuring that products are there when you need them and gone when you don't.
Setup your warehouse in 2 minutes with GoRamp for free.
Importance of logistics in manufacturing
Logistics is essential to your manufacturing operations for so many reasons. Here are some of them:
Cost efficiency
Cost efficiency is one of the most compelling reasons to get your logistics strategy right. A well-planned logistics system can save significant amounts of money at various manufacturing stages.
For example, bulk purchasing of raw materials can reduce costs, but only if there's efficient inventory management to ensure those materials get used before going bad or becoming obsolete.
Transportation is another area where costs can spiral if not carefully managed. For instance, the choice between short-haul and long-haul options can have a significant financial impact. Picking the suitable mode of transportation based on factors like delivery time, volume, and fuel costs can make a real difference to your bottom line.
And let's not forget warehousing. Using smart layout designs or adopting warehouse management solutions can prevent space wastage. Sometimes, outsourcing these tasks to a 3PL provider can be more cost-efficient than managing them in-house.
Time management
In manufacturing, poor logistics can lead to delays that ripple through the entire supply chain, disrupting your operations and affecting customer satisfaction. That's why time management is critical to consider when optimizing your logistics.
For example, efficient dock scheduling can avoid bottlenecks when goods arrive or are dispatched from the warehouse. A Warehouse Dock Scheduling Software can further streamline these processes by providing real-time updates and facilitating quicker decision-making.
But it's not just about speed; it's about timing. Last-mile delivery, the final step in the supply chain, often requires precision timing to meet customer demands. Getting the timing right is crucial, whether it's a two-hour delivery window or coordinating with other supply chain partners.
Quality control
Quality is a non-negotiable factor in manufacturing. You might get all the other elements right, but if the end product doesn’t meet quality standards, all that effort can go to waste. Logistics plays an integral role in maintaining and even enhancing product quality.
For starters, inventory management systems can help ensure that raw materials and finished products are stored optimally to prevent deterioration. Having controlled environments within warehouses can preserve the integrity of sensitive goods, thereby maintaining quality.
Transportation is another area where quality can be compromised if logistics aren't carefully managed. Incorrect handling during transit or delays leading to spoiling perishable goods can be disastrous.
Logistics challenges in manufacturing companies
Logistics in the manufacturing industry isn't all smooth sailing. There are common challenges that can disrupt even the most well-thought-out systems. Below are some of these logistics challenges and practical ways to overcome them:
Fluctuating Demand
Challenge: Handling fluctuating demand can be a nightmare in logistics management, affecting everything from inventory levels to transportation availability.
Solution: Implement a robust forecasting system that uses historical data and market trends. Consider using Just-in-Time (JIT) to reduce in-process inventory and associated costs. For perishables, consider a First-In-First-Out (FIFO) approach to reduce waste.
Supply Chain Visibility
Challenge: A lack of real-time visibility into your supply chain can lead to inefficiencies and increased costs.
Solution: Invest in technology that tracks shipments and inventory levels. This can include GPS tracking for shipments and RFID tags for inventory. Use dock scheduling software to manage arrivals and departures and plan for contingencies like traffic delays with buffer times.
Compliance and Regulations
Challenge: Regulations can be complex and time-consuming, especially for international shipments. You don’t want to get a call that your shipment got held up at a European port because you weren't aware of a new environmental compliance requirement.
Solution: Keep a checklist of international compliance standards and update it regularly. The best way to do this is to automate the documentation process or assign a compliance officer who can stay on top of new regulations and save you potential legal troubles.
Last-Mile Delivery
Challenge: Last-mile delivery is often the most complex and expensive part of the logistics process. Frequent customer complaints about late or missed deliveries affect your brand's reputation.
Solution: Opt for localized distribution centers and leverage route optimization software to minimize costs and delivery times.
High Transportation Costs
Challenge: Rising fuel prices and other variables can drastically affect the cost-effectiveness of your logistics. For example, air freight costs have increased by 10% and blown your logistics budget for the quarter.
Solution: Consider different transportation methods, such as short-haul vs long-haul, and weigh their pros and cons with your specific needs. Also, bulk shipments and off-peak scheduling can result in cost savings.
Limited Resources
Challenge: Small to medium-sized manufacturers often operate with limited resources, making it difficult to manage a sophisticated logistics operation.
Solution: Consider outsourcing specific logistics functions to Third-Party Logistics (3PL) providers who can provide expertise and resources you may not have in-house.
How Dock Scheduling Software can improve manufacturing logistics
Dock scheduling can often be a hidden bottleneck in logistics operations. It might seem simple—just coordinating when trucks arrive and depart—but in reality, it's a complex task with far-reaching implications.
Dock Scheduling Software can offer a solution that makes this aspect of logistics manageable and optimized. When you have a digital system in place for scheduling, you reduce the risks associated with human error, like double-booking or overlooking time-sensitive shipments. This alone can speed up your entire logistics process, cutting down on delays and the associated costs.
The software can also adapt to real-time changes, like a truck getting delayed on its route. Instead of the whole system getting bogged down, adjustments can be made on the fly to keep things running smoothly. This adaptability is a significant asset in maintaining a seamless logistics operation.
GoRamp’s Dock Scheduling Software helps companies eliminate queues in the production line, streamline truck check-in & automate communication.
Book a quick demo to get started.