The OTIF metric is a standard for efficiency and customer satisfaction in supply chain logistics. This key performance indicator (KPI) tracks delivery success and represents a bundle of other intimately related logistics activities like inventory accuracy and customer needs.
As supply chain businesses deal with escalating costs associated with missed deadlines and incomplete shipments, OTIF is their lifeline back to smoother operations. In this article, we’ll unpack how companies can successfully understand and implement OTIF standards and turn problem areas into new opportunities for optimization and better levels of customer satisfaction.
What is OTIF?
OTIF stands for "On-Time In-Full," a critical metric supply chain managers use to assess supplier performance by measuring whether or not deliveries are made correctly, completely, and at the agreed or scheduled times.
The metric is divided into two main components: "On-Time" refers to orders arriving within the specified delivery window (on-time delivery), while "In-Full" means that the entire order arrives without any missing or incorrect items. (order fulfillment).
The significance of OTIF in supply chain operations is substantial. A high OTIF score indicates a reliable, efficient supply chain that minimizes disruptions and maximizes customer satisfaction. Conversely, low OTIF performance can lead to many problems for the shipper, whether that be a supplier, manufacturer, or another. These problems include increased costs from expedited shipments, lost sales, and even strained relationships with retail partners.
This metric serves a dual purpose. It acts as a snapshot of supplier reliability while simultaneously functioning as a vital KPI (Key Performance Indicator) to identify areas for improvement. Moreover, OTIF holds weight in decision-making processes such as vendor selection, inventory planning, and even the negotiation of trade terms. Its utility is expansive, making it an invaluable tool in the arsenal of supply chain metrics.
How is OTIF calculated?
The calculation of OTIF is very straightforward, and it is calculated as a percentage The formula for OTIF is:
OTIF = (Number of On-Time, In-Full Deliveries / Total Number of Deliveries) x 100
The numerator represents the number of shipments that arrived on time and in full, while the denominator stands for the total number of shipments made. Multiplying the ratio by 100 gives you the OTIF rate in percentage form, providing a quick but powerful snapshot of your operational effectiveness.
Understanding the OTIF percentage is crucial for benchmarking your performance and setting actionable goals to achieve higher supply chain efficiency.
The OTIF formula may be simple, yet it's one of the most impactful metrics in supply chain logistics, reflecting both reliability and effectiveness.
How can you improve OTIF?
Improving your OTIF score involves a holistic approach that focuses on various stages of the supply chain. Here are some actionable insights:
- Advanced planning: Work closely with your suppliers and coordinate effectively. Make sure to have a solid forecast and place orders well in advance to ensure on-time production and shipping.
- Effective communication: Foster a culture of open dialogue with your suppliers and transport partners. Regular check-ins and status updates can help preempt problems before they cause delays or incomplete orders.
- Technology integration: Utilize a Transportation Management System (TMS) with real-time tracking and analytics. These tools can provide immediate data on shipment status, helping to predict and avoid delays. Additionally, automated alerts can notify you when a shipment is off-course, allowing for immediate action.
- Audit regularly: Make it a practice to audit your OTIF performance, both internally and with your suppliers. Identify the root causes of failed deliveries and collaborate on corrective action plans.
- Vendor compliance: Establish clear guidelines and performance expectations with vendors. Non-compliance should result in re-evaluation of the partnership or contractual penalties.
- Inventory management: Keep an eye on stock levels and employ just-in-time inventory practices to ensure you have what you need when needed, but without excessive holding costs.
- Process optimization: Examine your internal processes for picking, packing, and shipping. Streamlining these can significantly reduce the chance of human errors, a common cause of incomplete deliveries.
- Data-driven decision-making: Dive deep into your metrics, beyond just the OTIF rate, to understand performance drivers. Utilize data to prioritize areas for improvement and to measure the impact of changes made.
Improving OTIF is a multi-faceted effort requiring coordinated action across several supply chain touchpoints. Focusing on these areas can elevate your OTIF performance and enhance overall supply chain efficiency.
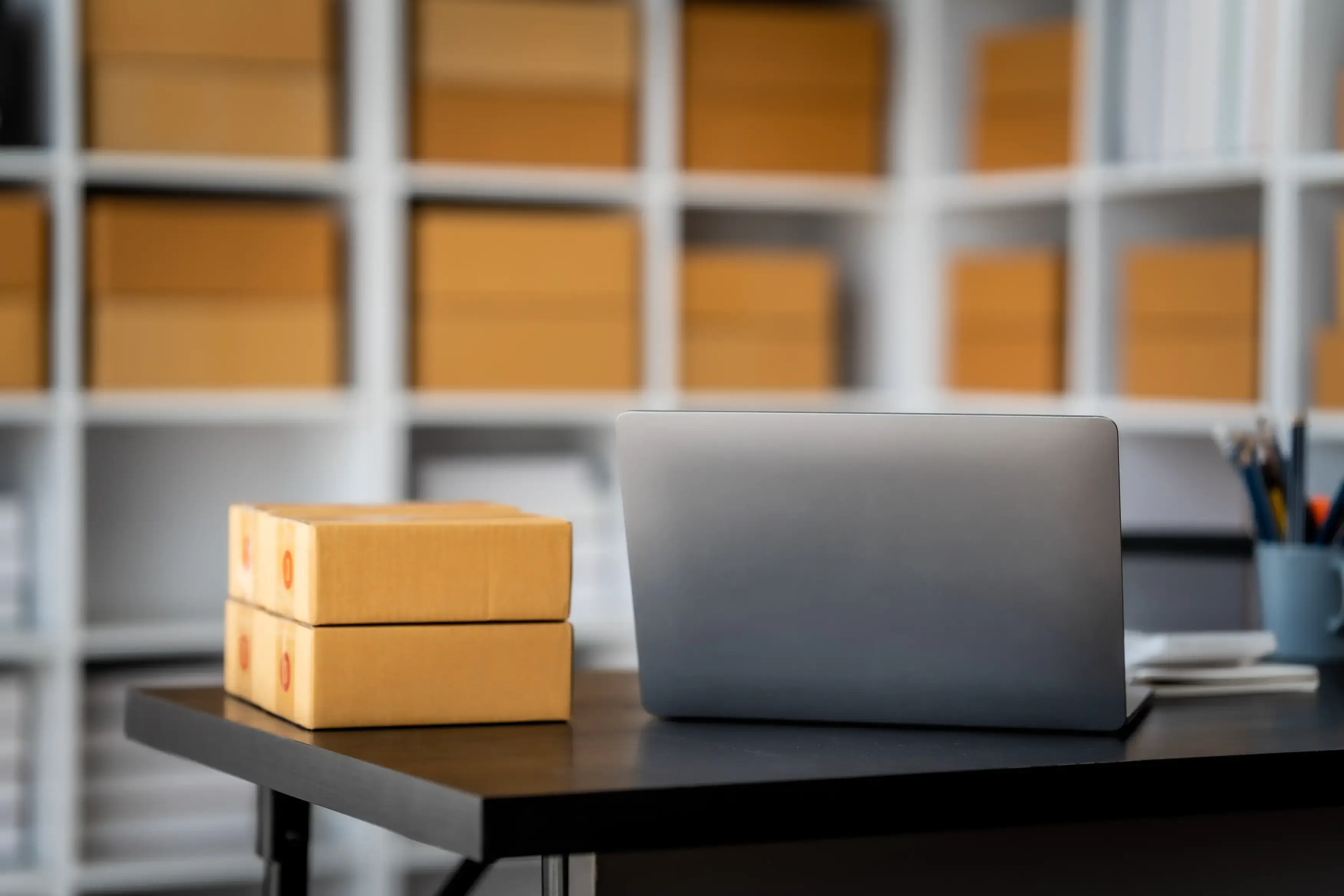
Adapting in real-time to avoid OTIF delivery fines
Navigating the complexities of supply chain operations requires agility, especially when avoiding OTIF delivery fines. Penalties can significantly erode margins, making real-time adaptation crucial for operational viability. Here's how to make timely adjustments to mitigate these costs:
Real-time tracking
Utilize tracking technology integrated within your TMS for real-time updates on shipment locations. Being informed enables you to take immediate action if a shipment appears to be running late.
Dynamic routing
Incorporate dynamic routing capabilities into your transport management. This technology can reroute shipments in real time to avoid delays due to unforeseen issues like traffic or weather conditions.
Predictive analytics
Employ tools to forecast potential delays based on historical data and real-time variables. These insights allow you to take preemptive measures.
Automated alerts
Implement a system of automatic alerts that notify key stakeholders of impending delays or discrepancies. Quick notifications allow for immediate remedial actions.
Carrier collaboration
Maintain open lines of communication with your carriers. Shared dashboards or mobile applications can facilitate real-time coordination, enabling quicker responses to emerging issues.
Escalation protocols
Have a defined set of escalation protocols for dealing with OTIF-related emergencies. Make sure all team members are aware of these procedures and trained to act promptly.
Contingency planning
Always have a contingency plan ready. Whether it's expedited shipping options or emergency stock levels, being prepared with alternatives can help avoid fines.
Real-time adaptation aims to build a responsive and agile supply chain infrastructure that minimizes risks and optimizes performance. By employing these strategies and leveraging appropriate tools, you can significantly reduce the risk of incurring OTIF delivery fines.
How OTIF affects stakeholders
OTIF takes on distinct yet complementary meanings for different stakeholders, primarily retailers and manufacturers.
For retailers, a high OTIF score translates to assured product availability, enhancing the customer experience and bolstering brand reliability. Retailers seek to stock shelves promptly, and a lack of adherence to OTIF standards can lead to stockouts or overstock situations, affecting sales and profitability.
Manufacturers, on the other hand, view OTIF as an indicator of operational efficiency and a measurement of how well they can meet or exceed their commitments. Meeting OTIF criteria consistently allows manufacturers to streamline supply chain and foster stronger, more reliable relationships with retailers. Failure to meet these criteria can result in loss of business, as retailers may opt to work with more reliable suppliers to avoid stockouts or excess inventory issues.
The value of OTIF lies in its ability to create a seamless flow of goods, benefiting both retailers and manufacturers. When the chain operates smoothly, the ripple effect can be felt from production lines to store shelves. For retailers, it increases customer satisfaction and loyalty, and for manufacturers, it provides critical feedback loops for continuous improvement and long-term success.
Use visibility and metrics to optimize OTIF performance
In the pursuit of optimizing OTIF performance, visibility and focused metrics emerge as crucial elements.
Visibility into each stage of the supply chain allows stakeholders to identify bottlenecks, delays, or inefficiencies in real-time. Technologies like real-time tracking and advanced analytics platforms offer a granular view of operations, enabling quick decisions and proactive measures.
For example, if a shipment is delayed at a port, immediate visibility allows for swift re-routing or rescheduling to minimize the impact on OTIF scores.

Focused metrics serve as the cornerstone for performance assessment and continuous improvement. Rather than attempting to monitor all KPIs, concentrate on those directly affecting OTIF scores. These might include 'Dock-to-Stock Time,' which measures how quickly goods move from receiving to available inventory, or 'Perfect Order Percentage,' capturing the proportion of orders that meet all desired criteria, from accuracy to condition and timeliness.
Regularly assessing and calibrating these metrics enables precise interventions, turning the data into actionable insights.
Integrating visibility and metrics creates a more cohesive and effective OTIF strategy. Enhanced visibility provides the data, while focused metrics give that data context, guiding efforts for improvement. Using these combined tools, organizations can meet and exceed OTIF requirements, benefiting all stakeholders involved.
It's about striking a balance between data collection and data utilization, ensuring the right information is available and actionable, and setting the stage for sustained OTIF success.
Track operational efficiencies with GoRamp
Efficiency, reliability, and tracking performance are the pillars of modern supply chain management. GoRamp works as a catalyst in achieving these objectives. The platform is engineered to offer an all-encompassing view of your supply chain, pulling together freight management, real-time tracking, and document handling into one centralized interface.
With a track record of enhancing operational outcomes across efficiency sectors, GoRamp is a versatile tool that can meet a broad spectrum of demands. Its sophisticated technology streamlines multifaceted operations, granting businesses the focus they need to excel in the core areas outlined in this article. Choosing GoRamp to bolster your OTIF performance brings technological advancement to your business and delivers a sustainable pathway to operational excellence.
Schedule a personalized demo and discover how you can take your supply chain performance to the next level.