Beginning a new workweek on a positive note, we're excited to share another success story from one of GoRamp’s esteemed customers. Adrija Bakanė, the Logistics Service Manager at IMLITEX HOLDINGS, shares their journey of implementing GoRamp’s Warehouse Management System (WMS) in their Lithuanian warehouses.
IMLITEX HOLDINGS, a leading commodity and raw materials distribution group in Eastern Europe, operates across nine business segments, including agriculture, biofuel, energy, food, industry, packaging, plastics, services, and textiles. With trade relations in 70 countries and a focus on European markets, the company handles an impressive 1.5 million tons of raw materials annually, generating a turnover of 350 million Euros.
Identifying IMLITEX' warehouse management issues
IMLITEX HOLDINGS, with its extensive operations across various sectors, faced a set of unique challenges in its warehouse management, which were impeding its logistics efficiency and overall productivity:
1. Truck congestions at the warehouse: The most pressing issue was the frequent congestion of trucks around the warehouse. This problem was twofold - it not only caused delays in loading and unloading but also led to significant logistical bottlenecks. The accumulation of trucks waiting to be serviced disrupted the planned schedules and often resulted in long, unproductive waiting periods for drivers.
2. Uneven distribution of daily Traffic: Another critical challenge was the uneven distribution of truck traffic throughout the day. This irregular flow resulted in periods of intense activity followed by times of underutilization, making it difficult to manage resources effectively. The inconsistent traffic flow strained the warehouse staff during peak times and led to inefficiencies in operations.
3. Complicated communication methods: The communication methods employed within the logistics operations were complex and outdated. This complication in communication channels contributed to delays in information dissemination and increased the likelihood of miscommunication. It also hindered the ability to respond swiftly to changes or issues, further exacerbating the congestion and scheduling problems.
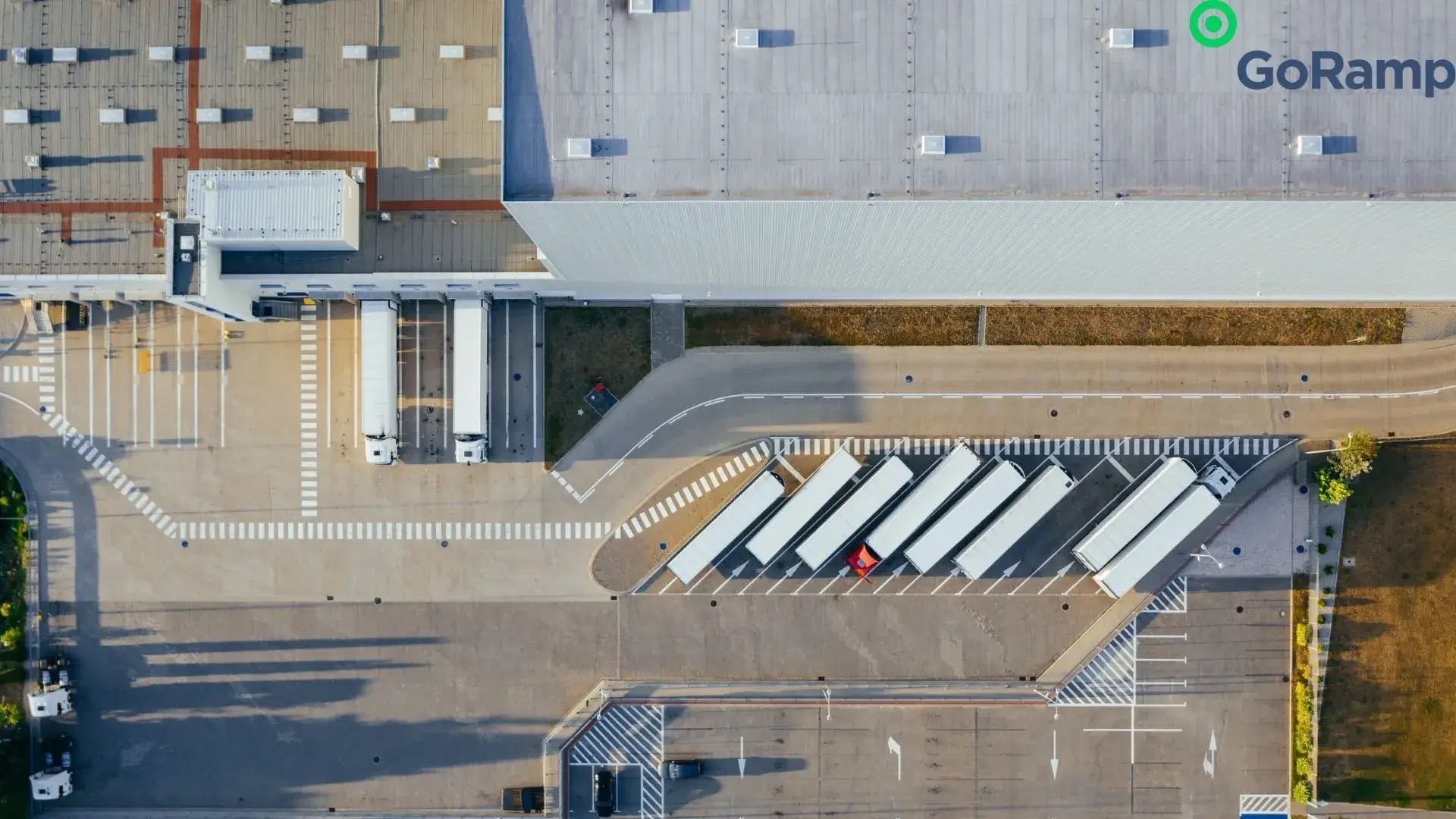
These challenges not only affected the immediate operations of IMLITEX HOLDINGS but also had a cascading effect on the broader supply chain, including potential penalties for transportation companies due to delays and inefficiencies. Addressing these issues required a comprehensive solution that could streamline processes, improve communication, and optimize the flow of traffic through the warehouse.
Implementing GoRamp's Time Slot Management System
To address these challenges, GoRamp proposed its Time Slot Management System, a digital WMS solution designed to optimize logistics processes. This system offered IMLITEX the tools to:
- Control warehouse scheduling: Enable booking of separate loading times and cap the number of operating ramps to prevent overloading.
- Centralize Information: Store all relevant logistics information in one location, facilitating easier access and decision-making for employees.
The implementation of GoRamp's Time Slot Management System significantly transformed the logistics operations at IMLITEX HOLDINGS. This change not only addressed their existing challenges but also propelled their warehouse management towards greater efficiency and productivity. The key areas of transformation included:
- Streamlined communication across the supply Chain: The introduction of GoRamp's system vastly improved communication methods within IMLITEX’s logistics operations. The platform provided a centralized hub for information, ensuring all stakeholders - from warehouse staff to transport companies - had access to real-time updates and clear instructions. This improvement in communication reduced misunderstandings and delays, leading to a more cohesive and efficient operation.
- Efficient management of truck traffic: One of the most significant changes was the efficient management of daily truck flow. The Time Slot Management System allowed for the scheduling of trucks at specific times, evenly distributing the traffic throughout the day. This scheduling not only reduced the previously common truck congestions but also allowed for better utilization of the warehouse staff and resources.
- Optimization of warehouse operations: With the new system, IMLITEX was able to cap the number of trucks being serviced at any given time, aligning their workload with the available capacity. This optimization led to a more orderly and manageable environment, significantly reducing the stress and rush associated with the previous congestions.
- Substantial time savings and increased productivity: As a direct result of these improvements, IMLITEX experienced a 25% reduction in operational time. This time saving translated into increased productivity, as the warehouse could handle more trucks efficiently without the need for extended hours. The streamlined process also meant that warehouse employees could work more effectively, contributing to overall job satisfaction.
- Enhanced relationships and reliability: The successful implementation and operation of the GoRamp system strengthened the relationships between IMLITEX and its partners. The increased efficiency and reliability of the warehouse operations improved trust and dependability among the carriers, enhancing IMLITEX's reputation as a reliable partner in the supply chain.
This transformation at IMLITEX HOLDINGS exemplifies the positive impact that a well-integrated warehouse management system can have on a company's logistics operations. The changes brought about by GoRamp's solution not only resolved immediate operational challenges but also laid the foundation for ongoing improvements and efficiencies in their supply chain.
A new chapter in warehouse management
One of the primary reasons for choosing GoRamp was its easy-to-use interface, crucial in industries like manufacturing. This user-friendliness played a significant role in the successful adoption and effectiveness of the system at IMLITEX.
IMLITEX’s experience with GoRamp's Dock Scheduling product showcases the transformative impact a well-integrated WMS can have on warehouse operations. Their story is a testament to the efficiency and productivity gains achievable through the right digital solutions.
For businesses grappling with similar challenges in logistics, such as truck congestions and complicated communication, GoRamp’s solutions offer a proven path to improvement. Register for a demo to explore how GoRamp can enhance your business operations.