Efficient warehouse management is very important in supply chain optimization, and key performance indicators (KPIs) are central to this process. Warehouse KPIs provide a precise, quantifiable measure of performance, offering valuable insights into every aspect of warehouse management—from inventory turnover to order fulfilment rates.
Understanding and effectively utilizing these KPIs enables businesses to identify areas for improvement, make data-driven decisions, and ultimately stay ahead in the dynamic world of supply chain management.
To that end, this article will help you comprehend the full spectrum of warehouse KPIs and the business impacts that will bring you closer to maximizing your supply chain potential and maintaining your competitive edge. To better understand your supply chain maturity level, we created a free supply chain quiz.
Inventory management KPIs
Inventory management ensures optimal stock levels and efficient resource utilization. It encompasses a range of KPIs, each measuring a different aspect of inventory control, from accuracy and turnover to carrying costs and shrinkage.
1. Inventory accuracy
Inventory Accuracy is defined as the degree to which the inventory data—quantity and location—matches the actual physical inventory in the warehouse. It is typically expressed as a percentage, where a higher percentage denotes a closer match between the records and the physical count.
(Number of Accurate Inventory Records / Total Inventory Records) X 100 = Inventory Accuracy Percentage.
This KPI measures how well a warehouse tracks and maintains its stock and is also a crucial indicator of the health and efficiency of the entire supply chain.
To effectively monitor and optimize inventory accuracy, establish a baseline, set target accuracy levels, and track performance over time. This involves regular analysis of discrepancies and identifying root causes for inaccuracies.
2. Inventory turnover rate
The Inventory Turnover Rate measures how often a company's inventory is sold and replaced over a specific period, typically a year. This KPI is central to evaluating the efficiency of inventory management practices and sales health.
Total Cost of Goods Sold / Average Inventory = Inventory Turnover Rate
Use this KPI to gain insights into the balance between inventory levels and sales performance, indicating whether inventory is being used effectively or if improvements are needed.
To effectively monitor and optimize the Inventory Turnover Rate, businesses should regularly compare it against industry benchmarks, assess trends over time, and adjust inventory strategies accordingly. This includes reviewing purchasing patterns, sales strategies, and inventory management practices.
3. Carrying cost of inventory
The carrying cost of inventory refers to the total costs of holding and storing unsold goods. These costs typically include storage fees, insurance, employee wages, depreciation, and opportunity costs.
(Total Carrying Costs / Total Inventory Value) X 100 = Carrying Cost of Inventory Percentage
This KPI is essential for understanding the financial impact of inventory storage and helps determine inventory management efficiency.
To adequately monitor and optimize the Carrying Costs of Inventory, businesses should regularly analyze each carrying cost component, identify areas where expenses can be reduced, and balance inventory levels to minimize unnecessary storage. Strategies may involve optimizing warehouse space, improving inventory turnover, and employing just-in-time inventory practices.
4. Inventory-to-sales ratio
The inventory-to-sales ratio measures the relationship between the amount of inventory a company holds against the number of sales being made. This ratio helps assess whether a business is carrying excess stock or has an appropriate amount of inventory to meet customer demand.
Total Inventory Value / Total Sales Value = Inventory to Sales Ratio
This KPI is an integral benchmark of inventory efficiency, reflecting how well inventory levels are aligned with sales trends.
Businesses should regularly analyze their sales patterns and inventory turnover to productively monitor and optimize the inventory-to-sales ratio. Aligning inventory levels with sales forecasts and customer demand patterns is crucial. This involves adjusting procurement strategies, managing stock levels more effectively, and potentially diversifying or streamlining the product range.
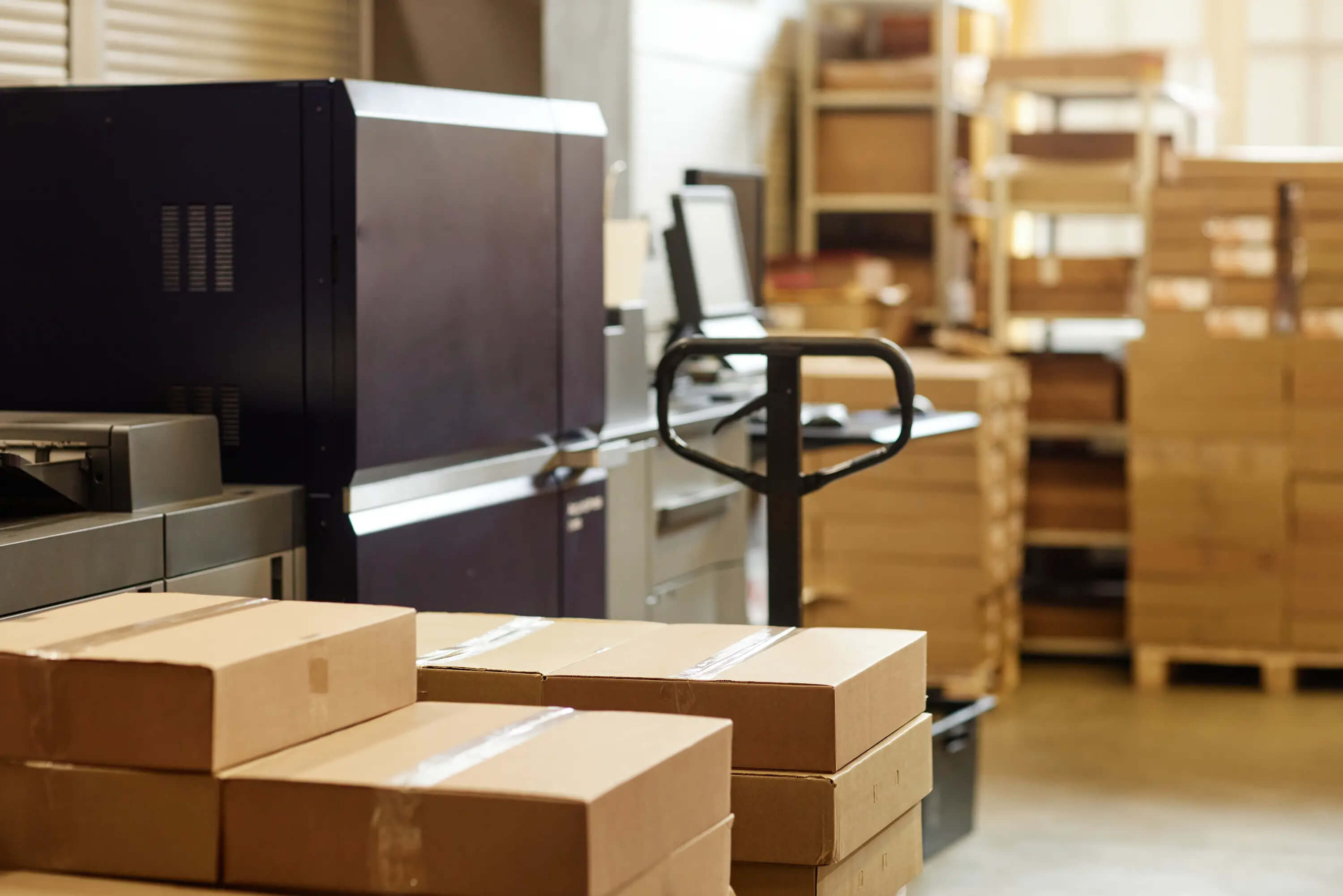
Order fulfillment and processing KPIs
This category focuses on various KPIs that measure the effectiveness of order processing, from the rate of fulfilling orders to the accuracy of picking them.
5. Order fulfillment rate
The Order Fulfillment Rate measures the percentage of customer orders that are fulfilled without stockouts or delays. It is an indispensable gauge of a company's ability to meet customer demand and maintain efficient inventory levels.
(Number of Orders Fulfilled / Total Orders Received) X 100 = Order Fulfillment Rate
This KPI assesses the effectiveness of inventory management and the efficiency of the order fulfillment process.
To precisely monitor and optimize the Order Fulfillment Rate, businesses should focus on accurate demand forecasting, efficient inventory management, and streamlined order processing. Regularly reviewing and adjusting inventory levels to match customer demand while ensuring timely procurement and efficient order processing are key to maintaining a high order fulfillment rate.
6. Backorder rate
The Backorder Rate is a key performance indicator that quantifies the percentage of customer orders that cannot be fulfilled immediately due to inadequate stock levels. It serves as a measure of how often a business faces stock shortages.
(Number of Backordered Items / Total Number of Ordered Items) X 100 = Backorder Rate
This KPI is vital for predicting customer satisfaction levels and assessing the effectiveness of inventory management.
Businesses should enhance their inventory forecasting accuracy, maintain optimal stock levels, and improve supply chain responsiveness to monitor and optimize the Backorder Rate effectively.
7. Order picking accuracy
Order Picking Accuracy measures the frequency at which items are correctly picked from the inventory against customer orders. This KPI is imperative in warehouse operations, giving management a line of sight into the reliability of their picking process.
(Number of Accurate Picks / Total Picks) X 100 = Order Picking Accuracy Rate
This KPI primarily evaluates the precision of order fulfillment and its downstream impact on customer satisfaction.
Competently monitoring and optimizing order-picking accuracy requires focusing on staff training, improving warehouse layout for easier access to items, and implementing quality control processes.
Warehouse efficiency KPIs
This category encompasses KPIs that assess the effectiveness and speed of various warehouse activities, from receiving goods to processing returns.
8. Receiving efficiency
Receiving efficiency measures the speed and accuracy with which goods are received, processed, and made ready for storage or sale in a warehouse. It's a key indicator of successful warehouse receiving operations.
(Total Units Received / Total Time Spent on Receiving) X 100 = Receiving Efficiency Percentage
Optimizing Receiving Efficiency metrics necessitates streamlining receiving processes, implementing efficient inventory management systems, and adequate staff training.
9. Putaway time
Putaway Time is a fundamental warehouse KPI that measures the duration from when goods are received in the warehouse to when they are stored in their designated location. This metric is key in assessing the efficiency of the storage process.
(Total Time from Receiving to Storage / Number of Items) = Average Putaway Time
To properly optimize Putaway Time, warehouses should focus on improving the layout for easy navigation, employing inventory management systems, and training staff for on storage workflows designed for speed and accuracy.
Streamlining the putaway process through methods such as cross-docking, where appropriate, and using technology like warehouse management systems (WMS) can significantly reduce putaway time and enhance overall operational efficiency.
10. Pick and pack cycle time
Pick and Pack Cycle Time measures the duration from the initiation of an order picking process to the completion of the packing stage, ready for shipment.
(Total Time for Picking and Packing / Total Orders Processed) = Average Pick and Pack Cycle Time
This KPI is instrumental in assessing the speed and efficiency of the picking and packing operations, directly impacting customer satisfaction and operational throughput.
To monitor and optimize pick-and-pack cycle time, focus on more efficient picking routes within the warehouse layout, implement advanced picking methods, and provide proper staff training. Using warehouse automation technology such as automated picking systems can significantly streamline this process, reducing cycle times and bolstering customer service levels.
11. Labor productivity (Units picked per hour)
Labor Productivity, specifically measured as Units Picked per Hour, quantifies the efficiency of warehouse staff in terms of the number of units they can pick within an hour. It’s a non-negotiable KPI for assessing workforce efficiency in a warehouse setting.
(Total Units Picked / Total Labor Hours) = Units Picked per Hour
This KPI gauges the effectiveness of the warehouse labor activities, impacting overall productivity and costs.
Thoroughly optimizing Labor Productivity requires a focus on warehouse layouts for accessibility, efficient picking strategies, and providing comprehensive training and incentives for staff to execute routines. Regular analysis of picking patterns, leveraging technology, and creating a supportive work environment are core factors in enhancing labor productivity.
Continuous improvement efforts and ergonomic considerations can also contribute significantly to increased units picked per hour and employee satisfaction.
Supply chain performance KPIs
These KPIs help monitor the supply chain's reliability and cost-effectiveness, focusing on aspects such as delivery accuracy, cost management, and supplier performance.
12. Rate of return (Return rate)
The Rate of Return, or Return Rate, is a KPI that measures the percentage of sold products that are returned by customers. This metric measures customer satisfaction and the quality of products or services provided.
(Total Number of Returned Items / Total Number of Sold Items) X 100 = Rate of Return Percentage
This KPI is diagnostic for understanding the reasons behind product returns, including quality issues, customer satisfaction, or order inaccuracies.
To benchmark the return rate, analyze the reasons for returns and implement measures to address these issues. This could involve enhancing product quality, improving order fulfillment accuracy, and providing better customer service.
13. Delivery lead time
Delivery Lead Time is a barometer in supply chain management, measuring the time taken from placing a customer order to delivering the product. It indicates the efficiency of the entire order processing and delivery system.
(Date of Delivery - Date of Order Placement) = Delivery Lead Time
Optimizing Delivery Lead Time requires businesses to streamline order processing, enhance logistical efficiency, and strengthen supplier partnerships. Strategies include improving inventory management, adopting faster shipping methods, and leveraging technology for order tracking and processing.
Routinely reviewing and adjusting supply chain processes based on performance data and customer feedback is necessary to reduce lead times and meet customer expectations.
14. Supplier order accuracy
Supplier Order Accuracy measures the proportion of orders received from suppliers that are accurate in terms of item type, quantity, and quality.
(Number of Accurate Supplier Orders / Total Supplier Orders) X 100 = Supplier Order Accuracy Percentage
This indispensable KPI impacts inventory management and production planning by assessing the precision and reliability of suppliers.
Supplier Order Accuracy optimization is achieved by establishing clear communication and agreements with suppliers, setting precise order specifications, and implementing quality checks upon receipt. Regular supplier evaluations, fostering strong supplier relationships, and employing technology for order tracking and verification can significantly enhance order accuracy. Address issues promptly and work collaboratively with suppliers to rectify inaccuracies.
15. Fill rate
The Fill Rate measures the percentage of customer orders that are fulfilled from the initial stock without backorders or delays. Primarily, this KPI provides insight into how well a company manages its inventory in relation to customer demand, which directly impacts customer satisfaction and sales efficiency.
(Number of Orders Fulfilled from Stock / Total Customer Orders) X 100 = Fill Rate Percentage
To effectively monitor and optimize the Fill Rate, businesses should focus on accurate demand forecasting, maintaining optimal inventory levels, and efficient order processing. Analysis of fill rates and adjustments in inventory replenishment strategies and warehouse operations achieve a high fill rate. Additionally, enhancing supplier relationships and exploring flexible inventory solutions can improve the ability to promptly and completely meet customer orders.
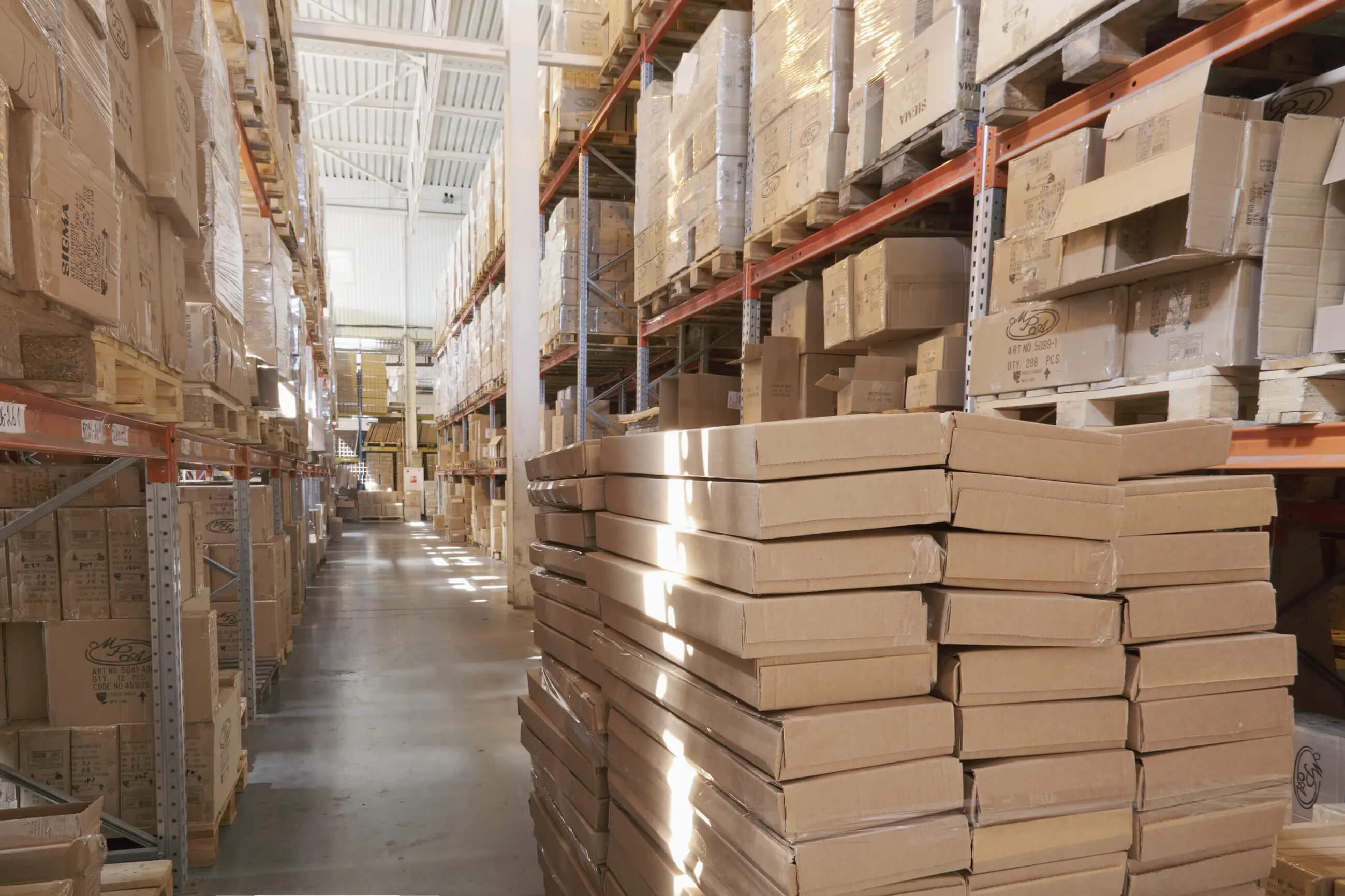
Quality and compliance KPIs
These KPIs measure product integrity, adherence to quality standards, safety, and related items, which are essential for customer trust and legal compliance.
16. Damage rate
The Damage Rate measures the percentage of products damaged in relation to the total products handled. It is a direct indicator of the quality of handling and storage processes.
(Number of Damaged Units / Total Units Handled) X 100 = Damage Rate Percentage
This KPI is paramount in assessing the adequacy of product handling and storage protocols, affecting cost efficiency and customer satisfaction.
To monitor and optimize the Damage Rate, businesses must implement stringent quality control measures, staff training on handling techniques, and ensure proper storage conditions. It’s imperative to routinely review handling procedures, invest in better packaging materials, and employ technology for safer and more efficient handling can significantly reduce the incidence of damage.
Maintaining a low damage rate will only occur by addressing the root causes of damage through process evaluation and other continuous improvement protocols.
17. Rate of return due to quality
The rate of return due to quality measures the percentage of products returned by customers specifically because of quality issues. Fundamentally, it assesses product quality and customer satisfaction levels.
(Number of Returns Due to Quality Issues / Total Number of Returns) X 100 = Rate of Return Due to Quality Percentage
This KPI is integral to pinpointing product quality shortcomings, which can affect brand reputation and customer loyalty.
To measure and gain insights related to the Rate of Return Due to Quality metrics, conduct thorough quality checks across all production processes prior to shipment. Analyze return reasons, customer feedback, and quality control data. With those insights, Improve manufacturing processes, quality assurance protocols, and supplier quality standards to reduce returns due to quality issues. Continuous product and process reviews are key to minimizing quality-related returns.
18. Audit score compliance
Audit score compliance is a key performance indicator that measures the degree to which a company adheres to industry standards, regulations, and internal policies as determined by audits.
(Audit Points Achieved / Total Possible Audit Points) X 100 = Audit Score Compliance Percentage
This KPI ensures the effectiveness of a company's compliance with industry, regulatory, legal, and internal quality requirements, impacting business credibility and operational integrity.
To monitor and optimize Audit Score Compliance, regularly review and update your business's operational processes to align with changing regulations and standards. Businesses must implement comprehensive training programs for staff and conduct regular internal reviews. Proactively addressing potential compliance issues, maintaining thorough documentation, and preparing diligently for audits can greatly enhance audit scores.
Achieving high levels of audit score compliance means there must be a culture of compliance and quality that is supported by consistent leadership and clear communication.
19. Safety incidents rate
The Safety Incidents Rate is a crucial KPI that quantifies the frequency of safety-related incidents within a workplace, such as accidents or near-misses. This is an essential metric for tracking workplace safety and the effectiveness of safety protocols.
(Number of Safety Incidents / Total Number of Hours Worked) X 100 = Safety Incidents Rate
To effectively evaluate the safety standards in an organization and optimize the Safety Incidents Rate, it’s vital to enforce rigorous safety guidelines, conduct regular safety training, and maintain a safe working environment. Routine safety audits, risk assessments, and employee engagement in safety practices are non-negotiable with this KPI.
Investing in safety equipment, enhancing workplace ergonomics, and fostering a culture of safety awareness can significantly reduce the incidence of safety incidents. Promptly addressing any identified safety concerns and continuously seeking ways to improve safety standards are essential to maintaining a low safety incidents rate.
%2520(1).jpeg)
Cost management KPIs
Cost management KPIs are vital for monitoring and controlling the financial aspects of warehouse operations. These indicators help businesses track expenses like warehousing, goods sold, and energy costs, ensuring profitability and efficient resource utilization.
20. Total warehouse cost
Total Warehouse Cost is a comprehensive KPI that encompasses all expenses associated with the operation of a warehouse, including labor, utilities, rent, equipment, and materials handling costs. It provides a holistic view of the financial demands of warehouse operations.
The sum of all Warehouse Operating Expenses = Total Warehouse Cost
Monitoring and optimizing Total Warehouse Cost requires businesses to review and analyze each cost component, identifying areas where expenses can be reduced without compromising efficiency or quality. Strategies include optimizing space utilization, improving labor productivity, negotiating better rates with suppliers and service providers, and investing in energy-efficient technologies.
21. Warehouse rent as a percentage of revenue
Warehouse rent as a percentage of revenue is a key financial metric that measures the cost of warehouse rent relative to the total revenue generated by the business. This KPI helps assess how much of the revenue is consumed by warehouse rental costs.
(Warehouse Rent / Total Revenue) X 100 = Warehouse Rent Percentage of Revenue
Using this metric helps businesses understand the financial burden of warehouse operations on the overall revenue, influencing decisions on operational scaling and cost management.
Optimizing and monitoring Warehouse Rent as a Percentage of Revenue, businesses should evaluate their warehouse space utilization and consider strategies for greatest efficiency. Routinely assess the need for the current warehouse space versus revenue performance, explore cost-effective leasing options, and consider location and operational adjustments to save on costs.
Businesses must balance the size and location of warehouse facilities to optimize processes and minimize rent costs without impacting service levels.
22. Energy cost as a percentage of warehouse operating cost
Energy Cost as a Percentage of Warehouse Operating Cost measures the proportion of total operating costs in a warehouse attributed to energy usage, including electricity, heating, and cooling. It provides insights into the energy efficiency of warehouse operations.
(Energy Costs / Total Warehouse Operating Costs) X 100 = Energy Cost Percentage of Warehouse Operating Costs
This KPI is important for evaluating how energy consumption impacts the overall cost-efficiency of warehouse operations, influencing the warehouse’s sustainability and profitability.
Focus on implementing energy-saving measures and technologies to monitor and optimize Energy Cost as a Percentage of Warehouse Operating. Strategies include upgrading to energy-efficient lighting and HVAC systems, optimizing equipment usage, and implementing energy management systems.
Best practices when measuring KPIs
Accurately measuring and interpreting Key Performance Indicators (KPIs) must be emphasized for your KPI initiatives to be successful. Consider the best practices below to ensure the reliability and effectiveness of your KPI measurement process.
- Define clear objectives: Start by aligning KPIs with specific business goals. Clear objectives ensure that each KPI is relevant and contributes to the larger organizational strategy.
- Ensure data accuracy: Accurate data is the foundation of meaningful KPIs. Implement comprehensive data collection and management systems to ensure the integrity of the data used for KPI calculations.
- Regular review and update: The business environment is constantly evolving. Review your KPIs regularly to ensure they remain relevant to current market conditions and business objectives.
- Utilize the right tools: Leverage advanced data analytics tools and software for efficient KPI tracking. These tools can provide deeper insights and aid in predictive analysis.
- Comprehensive training: Ensure your team understands how to measure and interpret KPIs. Extensive training leads to more accurate data handling and insightful analysis.
- Balance between qualitative and quantitative data: While KPIs are primarily quantitative, incorporating qualitative data can provide context and deeper understanding, leading to better decision-making.
- Actionable insights: Focus on KPIs that provide actionable insights. Data is only as valuable as the actions it prompts, so prioritize KPIs that directly inform decision-making and improvement strategies.
Using GoRamp to Optimize Warehouse Performance
GoRamp's capabilities in inventory management, order processing, and efficiency metrics ensure that businesses can precisely monitor, measure, and optimize their warehouse operations in a best-practice fashion.
By leveraging GoRamp's comprehensive solutions, you can effectively navigate the complexities of warehouse operations through enhanced insights and improved decision-making.
Discover the transformative impact GoRamp can have on your warehouse operations. Schedule a demo today to unlock the full potential of your warehouse performance!