Understanding logistics KPIs is the gateway to optimizing and driving business growth for management professionals navigating supply chain logistics and its complexities. This article helps readers understand these KPIs and their role and impact across the supply chain.
We’ll examine the significant supply chain sectors and key KPIs in each area, illustrating their importance with real-world examples, how to calculate them, and the results they yield.
What are logistics KPIs?
In supply chains, where margins and delivery timelines are tight, logistics KPIs create perspectives managers can use to objectively and analytically consider their operations. By tracking specific aspects of supply chain operations, logistics teams can pinpoint and reveal more opportunities for improvement. These actionable insights, in turn, open new perspectives and empower businesses to foster cultures of continuous improvement and efficiency.
Understanding and implementing logistics KPIs is vital to meeting the sector's demands and enabling precise, competitive advantages and solutions. Successful supply chain managers know that they must create the opportunity for excellence when they work in an environment that doesn’t stop or wait for anyone.
Supply-side logistics KPIs
Supply-side logistics focuses on the efficient and effective movement of goods from suppliers to production or retail facilities. The performance indicators in this area measure how well the supply logistics process is managed, impacting overall supply chain performance.
1. On-time supplier deliveries
On-time supplier deliveries are defined as how frequently suppliers deliver goods and materials within the scheduled time frames. This metric is crucial for maintaining efficient production schedules and ensuring uninterrupted operations.
(Number of on-time deliveries / Total number of deliveries) X 100 = On-time Supplier Delivery Percentage.
This KPI measures supplier reliability and impacts the overall effectiveness of the supply chain. It is also a fundamental metric for assessing supplier performance and maintaining productive relationships.
To adequately track and refine on-time supplier deliveries, establish clear delivery benchmarks, regularly assess supplier performance against them, and identify improvement areas.
2. Supplier defect rate
Supplier defect rate is the percentage of products or materials received from suppliers that fail to meet the required quality standards. It is an integral metric for evaluating supplier quality and its impact on product standards.
(Number of defective items received / Total number of items received) X 100 = Supplier Defect Rate.
This KPI proficiently measures the quality control effectiveness of suppliers.
To systematically track and enhance the supplier defect rate, it’s crucial to consistently review the rate of defects in received goods and work collaboratively with suppliers to identify causes and implement corrective actions.
3. Average supplier lead time
Average supplier lead time is defined as the average duration suppliers take to fulfill an order from its placement to its delivery. This measure is an index of supply chain responsiveness and supplier efficiency.
(Total lead time for all deliveries / Number of deliveries) = Average Supplier Lead Time.
This KPI is also an indispensable criterion for evaluating supplier performance in relation to production planning.
To proficiently track and optimize average supplier lead time, systematically review supplier performance, and identify opportunities for process improvements.
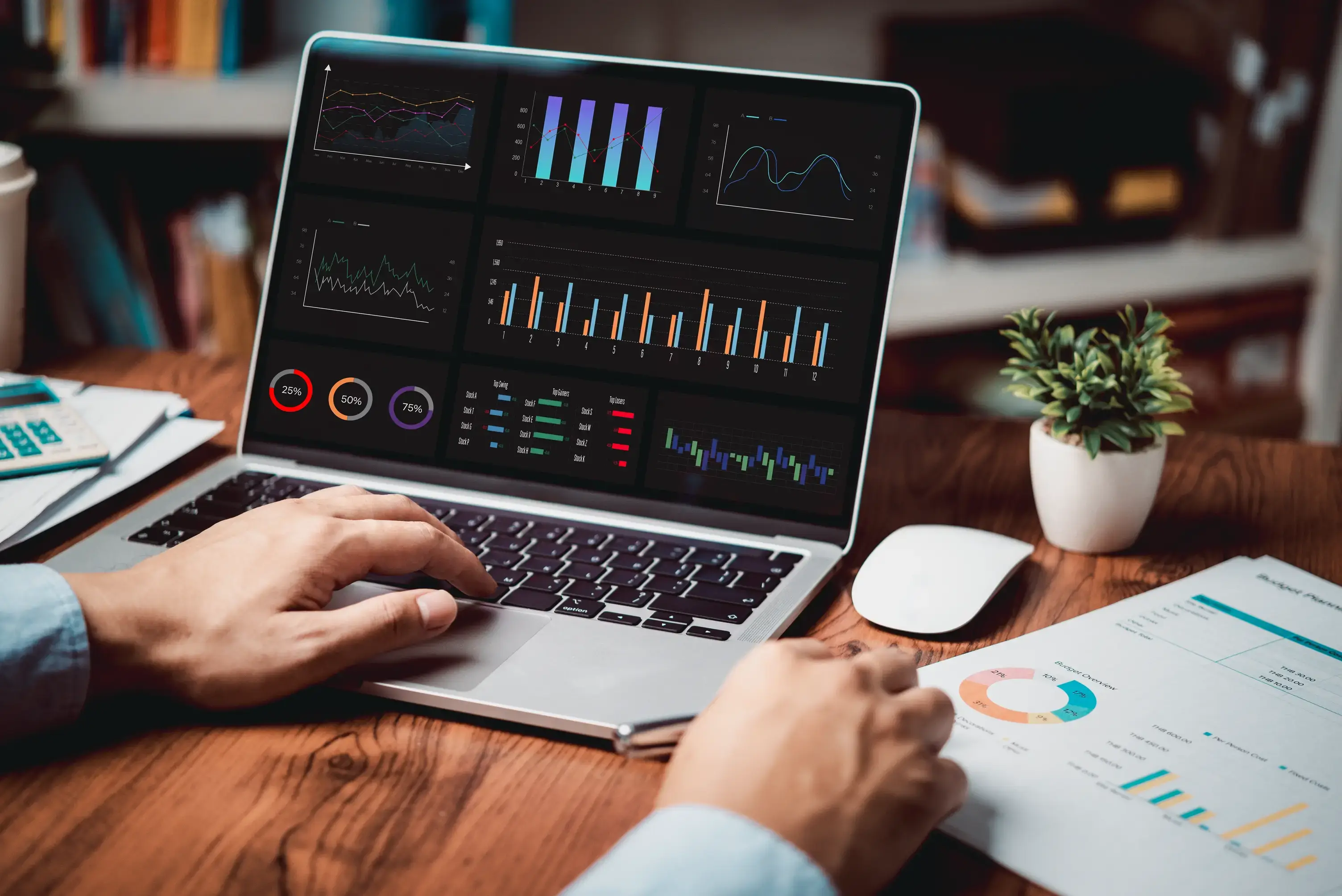
Order management KPIs
Order management logistics are pivotal in ensuring customer satisfaction and streamlining operational processes. These key performance indicators (KPIs) offer valuable insights into the effectiveness and efficiency of the order processing, fulfillment, and delivery systems.
4. Order cycle time
Order cycle time is the total time taken from placing an order to its completion and delivery to the customer. This metric is paramount to operational efficiency and customer service effectiveness in order processing.
(Total time from order placement to order delivery / Number of orders) = Order Cycle Time.
This KPI is for assessing the speed and efficiency of the order fulfillment process, directly influencing customer satisfaction and inventory turnover. It also helps in identifying bottlenecks in the order processing system.
To accurately track and refine order cycle time, it’s vital to set achievable cycle time goals, consistently assess performance against these goals, and systematically identify areas for process enhancement. This process includes a comprehensive review of each stage of the order process and collaborative efforts to eliminate inefficiencies and advance overall throughput.
5. Order accuracy rate
Order accuracy rate is the proportion of orders fulfilled correctly in terms of item type, quantity, and destination.
(Number of accurately fulfilled orders / Total number of orders) X 100 = Order Accuracy Rate.
This KPI measures operational excellence in order fulfillment, directly affecting customer trust and repeat business. It is also a vital measure for evaluating the effectiveness of your order management system.
To systematically track and enhance the order accuracy rate, it's essential to establish stringent accuracy standards, consistently monitor fulfillment processes against these standards, and identify key areas for improvement.
6. Backorder rate
The backorder rate is the frequency at which ordered items are unavailable for immediate shipment and require delayed delivery. This metric is critical to inventory management effectiveness and demand forecasting accuracy.
(Number of items on backorder / Total number of items ordered) X 100 = Backorder Rate.
This KPI is pivotal for assessing the balance between inventory supply and customer demand. It is also essential for evaluating the robustness of inventory planning and control mechanisms.
To proficiently track and minimize the backorder rate, it’s important to set realistic inventory levels, regularly analyze demand patterns, and systematically adjust inventory strategies.
7. Order processing time
Order processing time is determined as the duration from when an order is received until it is fully processed and ready for shipment. This metric measures the efficiency and responsiveness of the order-handling system.
(Time order is ready for shipment - Time order is received) = Order Processing Time.
This KPI is a crucial gauge for evaluating the speed and effectiveness of the order processing workflow, directly influencing overall customer experience and operational throughput.
To accurately assess and refine order processing time, it’s essential to establish a system for recording when the order is ready and when it is received. Using this data involves thoroughly analyzing each step in the order process and collaborating with the processing team to advance efficiency and reduce processing delays.
Inventory management KPIs
Inventory management is critical to optimizing supply chain efficiency and customer satisfaction. These key performance indicators (KPIs) help monitor and control inventory levels, ensuring the right balance between supply and demand.
8. Inventory turnover rate
Inventory turnover rate is quantified as the number of times inventory is sold and replaced over a specific period. This metric is an integral yardstick for evaluating the effectiveness of inventory management and product demand.
(Cost of Goods Sold / Average Inventory) = Inventory Turnover Rate.
This KPI is a key measure for assessing how efficiently inventory is managed and its alignment with market demand. It is also a fundamental benchmark for determining the balance between inventory holding and sales performance.
To track the inventory turnover rate, leverage advanced inventory management software for real-time tracking and regular inventory audits to ensure data accuracy. Analyzing sales trends and comparing turnover rates against industry benchmarks will allow you to understand demand patterns and optimize inventory levels.
9. Inventory accuracy
Inventory accuracy is the alignment between recorded inventory data—encompassing both quantity and location—and the actual physical inventory in the warehouse. It is typically expressed as a percentage, where a higher figure indicates a closer match between the records and the physical count.
(Number of accurate inventory records / Total inventory records) X 100 = Inventory Accuracy Percentage.
To systematically observe and improve inventory accuracy, regularly audit inventory records, pinpoint discrepancies, and identify root causes for inaccuracies to ensure continuous refinement of inventory management practices.
10. Days of inventory on hand (DOH)
Days of inventory on hand (DOH) is calculated as the average number of days that inventory is held before it is sold or used. This metric is vital for assessing inventory management efficiency and its alignment with production and sales cycles.
(Average Inventory / Cost of Goods Sold) X Number of Days in the Period = Days of Inventory on Hand.
This KPI is a crucial measure for evaluating how effectively inventory is managed in relation to sales activity. It is also a key index for determining inventory liquidity and its impact on cash flow.
To accurately track and optimize DOH, conduct a thorough and systematic analysis of inventory turnover rates and sales patterns, ensuring that inventory levels are balanced between market demand and operational requirements.
11. Stockout rate
Stockout rate is the frequency with which items are unavailable for sale or use when demanded by customers. This metric assesses inventory management effectiveness and the adequacy of stock replenishment strategies.
(Number of stockouts / Total number of items requested) X 100 = Stockout Rate.
To track and minimize the stockout rate proficiently, establish inventory monitoring systems, regularly review stock levels against demand forecasts, and implement proactive replenishment strategies.
12. Inventory carrying cost percentage
This is the proportion of total inventory costs, including storage, insurance, and taxes, relative to the total inventory value. This metric assesses the financial impact of holding inventory and its efficiency in terms of cost management.
(Total Inventory Carrying Costs / Total Inventory Value) X 100 = Inventory Carrying Cost Percentage.
This KPI is a crucial gauge of the economic efficiency of inventory management, highlighting the balance between the costs of storing inventory and its value.
To accurately track and refine inventory carrying cost percentage, it's important to regularly analyze inventory holding costs, compare them with inventory value, and identify opportunities for cost reduction.
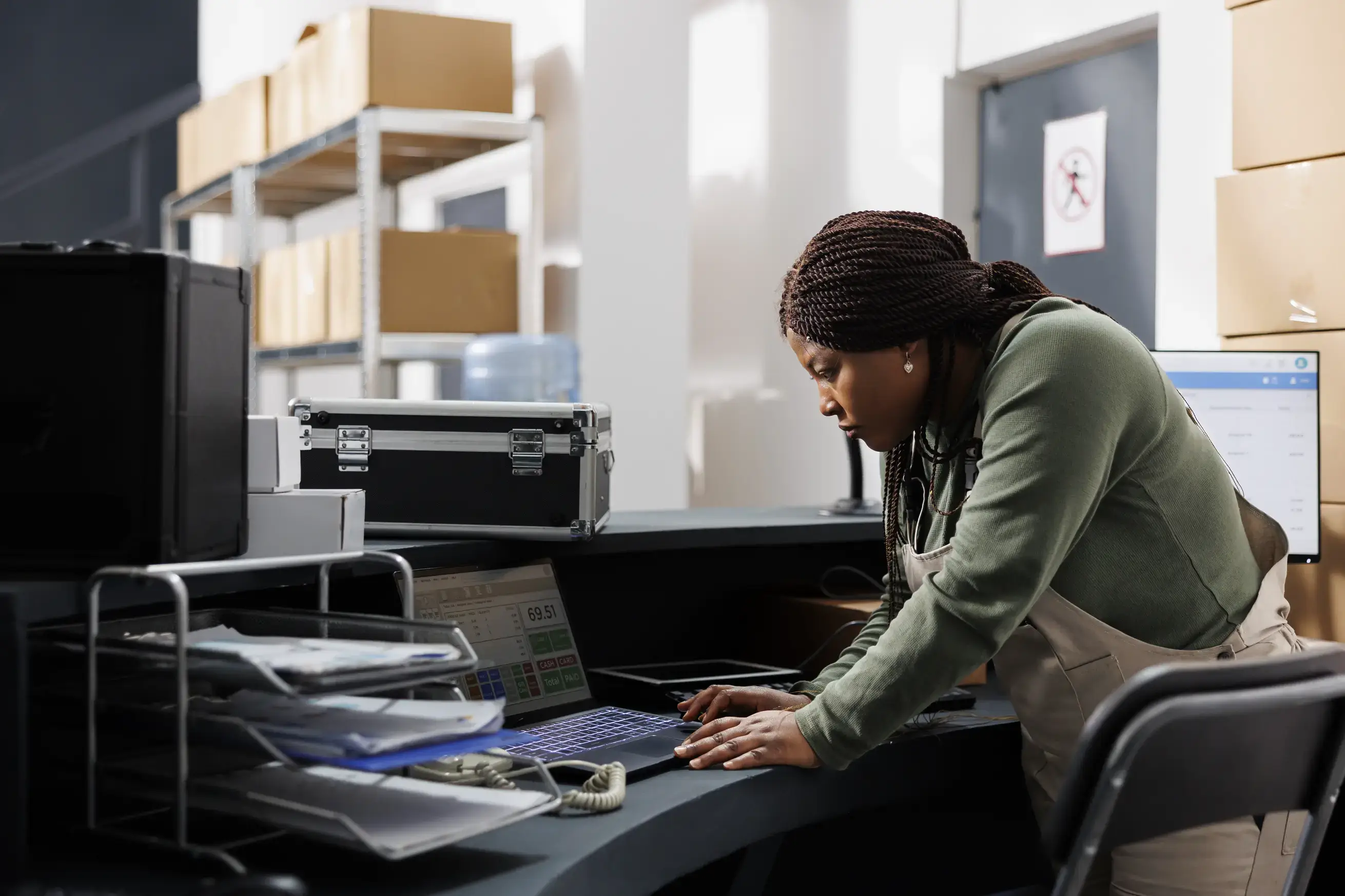
Transport management KPIs
Transport management is integral to supply chain efficiency and directly affects delivery times, costs, and customer satisfaction. Key performance indicators (KPIs) in this area help optimize transportation operations, from route planning to delivery performance.
13. Freight bill accuracy
Freight bill accuracy is measured as the proportion of freight bills that are free from errors in charges, classifications, and weights. This metric evaluates the billing process's precision and reliability in transportation management.
(Number of accurate freight bills / Total number of freight bills) X 100 = Freight Bill Accuracy Percentage.
This KPI assesses the accuracy of freight charges and the efficiency of the billing process, which directly impacts cost management and financial integrity.
It's essential to establish rigorous checking mechanisms for freight bills, consistently review billing accuracy, and implement corrective measures for discrepancies to track and maximize this completely. This process involves thoroughly scrutinizing billing processes, regular audits, and effective communication with carriers to rectify billing inaccuracies and enhance overall billing precision.
14. On-time delivery rate
The on-time delivery rate is calculated as the percentage of deliveries that arrive at their destination within the scheduled or promised time frame.
(Number of on-time deliveries / Total number of deliveries) X 100 = On-time Delivery Rate.
This KPI helps to assess the punctuality of delivery services, directly impacting customer satisfaction and trust. It is also an essential measure for evaluating the effectiveness of the logistics and distribution strategy.
To proficiently track and enhance the on-time delivery rate, set realistic delivery timeframes, consistently monitor delivery performance, and identify areas for logistical improvements.
This process involves a detailed analysis of transportation workflows, route optimization, and proactive management of potential delays to ensure timely and reliable product delivery.
15. Transportation cost per unit
Transportation cost per unit is the average cost of transporting each product unit. This metric is an essential gauge for evaluating the cost-effectiveness of transportation operations within the supply chain.
(Total Transportation Costs / Total Units Transported) = Transportation Cost Per Unit.
This KPI assesses how efficiently transportation resources are utilized, directly influencing overall logistics costs and pricing strategies. It is also a key metric for identifying opportunities to streamline transportation processes and reduce per-unit costs.
To effectively track this KPI, closely monitor freight invoices, accessorial charges, and cost-per-mile or cost-per-load for all modes of transport. Track fuel consumption and maintenance costs per vehicle and compare against mileage and payload to get cost per unit mile. Use transportation management software to get visibility into cost per shipment, cost per route, and cost per vehicle.
16. Average transit time
Average transit time is the average duration it takes for goods to be transported from the point of origin to their destination.
(Total Transit Time for All Deliveries / Number of Deliveries) = Average Transit Time.
This KPI evaluates the timeliness of the transportation system, which is crucial for maintaining inventory levels and meeting customer expectations. It is also an essential index for identifying areas where transportation processes can be streamlined or accelerated.
To set achievable transit time goals, consistently monitor transportation performance, and identify opportunities to reduce delays. This process involves a thorough review of transportation routes, carrier efficiency, and logistical planning, coupled with strategic actions to enhance the speed and reliability of transit operations.
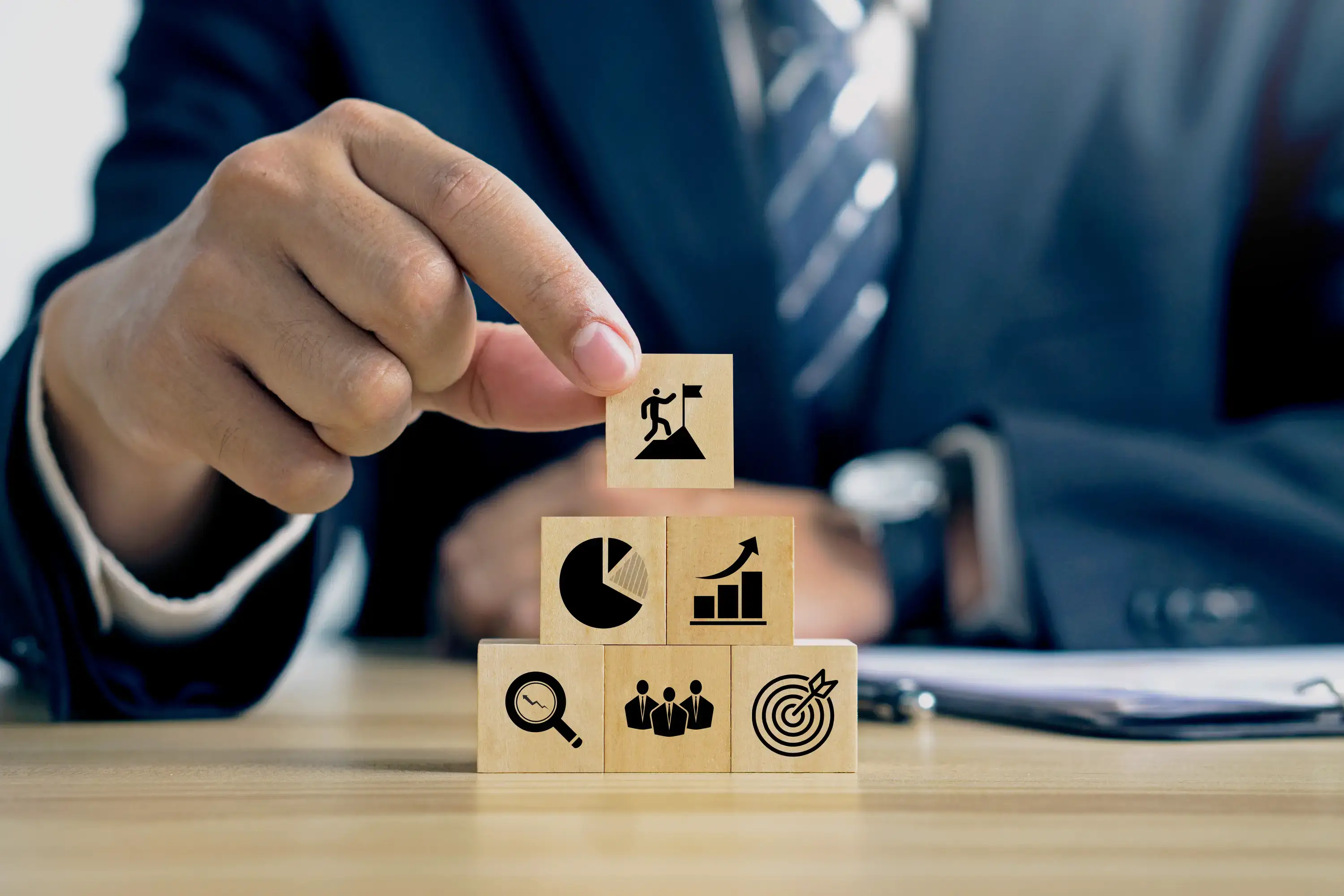
Distribution/Delivery KPIs
Distribution and delivery efficiency are crucial in supply chain management, impacting customer satisfaction, cost-effectiveness, and timely order fulfillment. KPIs in this sector track the performance of the distribution network and delivery systems.
17. Delivery lead time
Delivery lead time is the total time from when an order is placed until it is delivered to the customer. This metric assesses the delivery process's responsiveness and efficiency in meeting customer expectations.
(Order Placement Date - Delivery Date) = Delivery Lead Time.
To track delivery lead time, implement a logistics tracking system that records and calculates the duration from order placement to delivery. Regularly analyze delivery data to spot trends and inefficiencies, enabling proactive adjustments to optimize the delivery process.
18. Delivery accuracy rate
Delivery accuracy rate is quantified as the percentage of deliveries correctly executed in terms of item, quantity, and destination specifications. This metric is a central criterion for evaluating the precision and reliability of the delivery process.
(Number of accurate deliveries / Total number of deliveries) X 100 = Delivery Accuracy Rate.
This KPI is a fundamental gauge of operational excellence in delivery services. It directly affects customer trust and the supply chain's reputation. It is also a key measure for assessing the effectiveness of delivery systems and procedures.
To track delivery accuracy, implement a system that records and verifies the details of each order against customer deliveries to ensure precise data collection. Then, routinely analyze this data to calculate the rate of accurate deliveries compared to the total number of deliveries made.
Look for patterns or errors related to geographic areas, product-related issues, timing, and frequency, or performance-related problems.
19. Distribution cost as a percentage of sales
Distribution costs as a percentage of sales are calculated as total distribution expenses relative to total sales revenue. This metric is an essential gauge for assessing the cost-efficiency of the distribution process within overall sales performance.
(Total Distribution Costs / Total Sales) X 100 = Distribution Costs as Percentage of Sales.
This KPI evaluates how distribution costs impact sales profitability. It is also a key indicator for identifying opportunities to streamline distribution operations and improve the cost-to-revenue ratio.
Tracking distribution costs as a percentage of sales requires accurately recording all distribution-related expenses, including transportation, warehousing, labor, packaging, and comprehensive sales data. As you analyze this data, look for trends such as seasonal fluctuations in costs, price variations between different products, and cost percentages in relation to sales promotions or distribution strategies.
Assess if specific distribution channels or methods are consistently more cost-intensive than their contribution to sales—which will indicate areas to target for strategic adjustments.
20. Rate of return
The rate of return is defined as the percentage of orders returned by customers relative to the total number of orders fulfilled. This metric primarily indicates customer satisfaction and product or service quality.
(Number of Returned Orders / Total Orders) X 100 = Rate of Return.
A lower return rate typically indicates higher customer satisfaction and product suitability. It is also an essential gauge for identifying product development, delivery, or customer service areas that may require improvement.
In addition to maintaining detailed records of all returned orders and their reasons, perform the above calculation and analyze the data to look for specific patterns. For example, higher return rates for certain product categories can indicate quality or spec issues.
Also, look for returns clustering around certain times or seasons to determine if you must address your inventory management or shipping processes. Also, monitor if returns are more frequent with specific segments or sales channels. This could point to problems with targeted communication or expectation-setting.
Best practices when measuring KPIs
KPI measurement directly influences success potential in supply chain operations. To transform data into actionable insights and drive meaningful improvements, you must adopt a systematic approach to KPI measurement. Below are seven top-level best practices that will help frame your roadmap to measure KPIs accurately and leverage them for competitive advantage.
- Align KPIs with business objectives: It's imperative to ensure that KPIs directly support the broader business goals. Tailoring KPIs to reflect overarching objectives ensures they yield relevant and impactful insights for the business.
- Use a balanced approach: Integrating qualitative and quantitative KPIs creates a comprehensive view of supply chain performance. While numbers tell one part of the story, qualitative insights bring in the customer experience and workforce efficiency perspectives.
- Leverage technology for data collection: Modern technology is essential for gathering and analyzing data. Automated systems and AI analytics streamline the process and offer deeper, predictive insights.
- Train and involve the team: Building a data-centric culture starts with an informed team. When teams understand and engage with KPIs, data accuracy and the quality of insights improve significantly.
- Benchmark against industry standards: Comparing your KPIs to industry benchmarks provides a valuable perspective. It helps you identify competitive gaps and areas of excellence within your supply chain.
Using GoRamp to power KPIs and optimization
GoRamp is a transformative tool that catalyzes operational alignment and enhances the functionality of the KPI initiatives discussed in this article.
Forged by experts with deep knowledge of the industry's nuances, GoRamp bridges theoretical KPI optimization and practical application. Designed directly for supply chain management, its sophisticated technology streamlines logistics operations and provides the real-time data required to facilitate accurate and efficient KPI indicator tracking.
GoRamp’s platform is engineered to offer intuitive solutions addressing the complexities of modern logistics operations. By integrating GoRamp into their processes, businesses can monitor their logistics KPIs more effectively and make informed data-driven decisions that propel growth.
More than a data manager, GoRamp evolves logistics operations into a strategic asset that delivers advantages daily. Schedule a demo today!