Managing supply chain logistics requires understanding two central operations: inbound and outbound. You can frame nearly the entire logistical life cycle of goods, from their origin to their final destination, with an inbound or outbound operational lens.
In this article, we’ll explore inbound and outbound logistics. We’ll examine the distinct roles, challenges, and benefits each has within the supply chain. With this, you can re-evaluate your business’s inbound and outbound activities to develop a more nuanced perspective—which will sharpen your insights and reveal new advantages and opportunities.
What is inbound logistics?
Inbound logistics refers to the procurement, handling, and transportation of goods entering a business.
It's the first half of the supply chain, where resources and raw materials are gathered and delivered to warehouses, manufacturing plants, or retail stores. This phase is necessary for maintaining stock levels, and ensuring raw materials are available for production and products are present for consumers.
The driving mission of inbound logistics is the coordination of the activities below:
- Sourcing: Identifying and negotiating with suppliers to purchase goods or raw materials.
- Ordering: Determining the correct quantity of materials to order at the right time.
- Transportation: Selecting the most efficient method for receiving goods. This could involve various modes such as shipping, trucking, rail, or air, depending on distance, cost, and urgency.
- Receiving: The process of accepting deliveries, inspecting them for accuracy and quality, and preparing them for storage or production.
- Warehousing: Storing goods until they are needed for production or sale. This involves managing space effectively to keep inventory easily accessible and organized.
- Inventory management: Keeping track of stock levels, predicting when replenishment is needed, and avoiding shortages and excesses.
Inbound logistics is an intricate operation where precision in planning and execution can yield notable cost savings and increases in efficiency. Each item above has its own complexities, which all interface with processes and activities from other items on the list. It gets incredibly complicated. But that’s why so much gets overlooked regarding efficiency and the related opportunities more data and insight provide—unless you have superpowers or a cloud-based software system, it's impossible to keep track.
Read this for more insight on what you can gain from real-time data and analytics software.
What is outbound logistics?
Outbound logistics refers to the movement of finished goods from a company to the end user.
It’s the second half of the supply chain where products are delivered, and the brand’s value and reliability are put to the test. This is a critical phase impacting customer satisfaction and retention.
The outbound process starts once a product is manufactured and ready for dispatch. It involves several steps, beginning with order processing, where customer orders are confirmed and prepared for shipment. This step must be precise, as errors here lead to incorrect deliveries, increased returns, and damaged customer relationships.
Following order processing, warehouse management systems (WMS), if used, play a pivotal role in locating the items within a warehouse and managing the picking and packing. This system ensures that the correct products are shipped at the right time. Efficiency is crucial for maintaining the product flow and deliveries to meet customer expectations.
Next comes the handling and transportation, which can range from simple to complex depending on the product and destination. During this stage, logistics teams must decide the most cost-effective and efficient route for delivery, often involving coordination with third-party carriers.
Last-mile delivery, the final step in outbound logistics, is where businesses can distinguish themselves. It's the point where the product reaches the customer's doorstep—and people see the logos on the delivery truck and build opinions about your brand. Delays or mishandling here can severely impact customer satisfaction and reputation. However, optimal results can enhance the overall customer experience and increase the likelihood of repeat business.
Effective outbound logistics delivers products in a way that upholds the quality and service standard promised by a brand and expected by its customers. It’s a visible, tangible representation of a company's reliability and customer commitment. Therefore, optimizing these steps and procedures fosters trust and loyalty with the end consumer.
Take a look at how FUDO, a leading enterprise in the Baltic region, transformed its warehouse ops using GoRam’s warehouse management system.
What’s the difference between inbound and outbound logistics?
The difference between inbound and outbound logistics is foundational to the architecture of supply chain management. While both are sides of the same coin, they operate in distinct phases and have separate objectives, challenges, and processes.
Strategic differences
Inbound logistics’ strategic aim is to ensure the availability of materials necessary for production or sales without overstocking, thus minimizing holding costs and maximizing space utilization. It centers on the procurement, movement, and storage of raw materials and partially or fully finished products from suppliers to manufacturing or warehouse facilities. It’s a receptive process concerned with internal operations, including sourcing, supply chain sustainability, cost efficiency, and inventory management.
Outbound logistics’ objective is to maximize customer satisfaction and loyalty by ensuring products are delivered on time and in perfect condition, directly influencing the customer's experience with the brand. It centers on the outward flow of final products from the company to the end user. It encompasses everything from order processing to last-mile delivery.
Operational differences
Operationally, inbound logistics demands a harmonious relationship with suppliers and an analytical approach to demand forecasting and inventory levels. It requires focusing on inward efficiency and readiness to supply the business’s operational needs.
On the other hand, outbound logistics requires a dynamic approach that adapts to changing customer needs, emphasizing service, quality, and delivery performance.
Tactical differences
Tactically, inbound logistics might negotiate bulk shipping rates with suppliers, while outbound logistics seeks to optimize delivery routes and times. The KPIs also differ—inbound logistics might prioritize inventory turnover rates, whereas outbound logistics focuses on delivery times and order accuracy.
The tactical challenge for inbound logistics lies in synchronizing supply with demand, ensuring timely procurement and transportation to avoid disruptions while optimizing inventory levels and storage costs.
The tactical challenge for outbound logistics is to maintain the integrity of the product while navigating the complexities of distribution networks.
Understanding these differences is critical for businesses looking to engage and optimize their logistics strategies to improve performance, solicit cost savings, and bolster customer satisfaction.
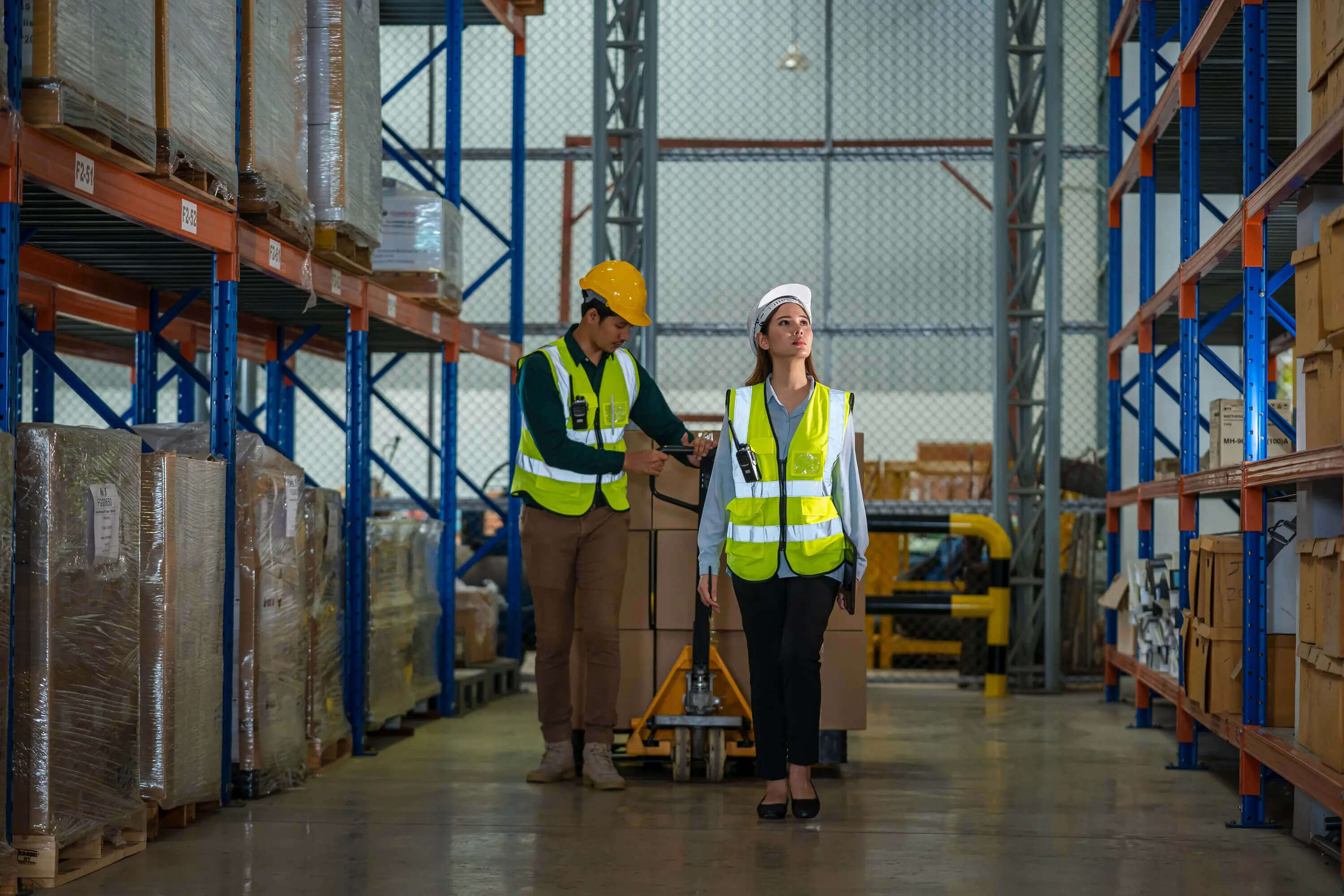
Inbound and outbound logistics processes
Efficient logistics processes form the structure and integrity of successful supply chains. Outlining the steps involved in inbound and outbound logistics presents a framework for gaining line-of-site on what needs doing to increase everything from efficiency to customer satisfaction.
Want to know when and how to modernize your warehouse logistics? A must-read.
Steps in inbound logistics
Sourcing: The beginning of inbound logistics lies in sourcing, where businesses strategize to procure raw materials or finished products. The focus is on quality, cost, and reliability, as procurement decisions directly impact production and cost management processes. Businesses must balance their sourcing strategy between maximizing cost-effectiveness and maintaining operationally sustainable supply chain practices.
Ordering: This step converts sourcing decisions into action. Companies issue purchase orders, aligning delivery timelines with their inventory requirements. Precision in this stage minimizes overstocking or stockouts, aligning with lean inventory methodologies.
Transporting: Transporting goods from suppliers to the company involves selecting suitable carriers, negotiating rates, and scheduling deliveries. Efficient transportation is a balance of cost, reliability, and speed. Companies must also navigate the complexities of customs and regulations for international shipments.
Receiving: Upon arrival, goods undergo quality checks to meet the specified standards. This step is critical for maintaining the integrity of the supply chain, as any discrepancies can significantly impact the downstream processes.
Inventory management: Proper inventory management involves storing goods in a manner that optimizes space utilization, preserves product quality, and allows for easy access. This stage is crucial for maintaining the flow of goods without interruption and readying them for production or direct shipment.
Steps in outbound logistics
Order processing: Once customers place orders, the processing stage engages, involving order validation, payment processing, and initiating the fulfillment process. Accuracy in order processing is vital to prevent errors that could lead to customer dissatisfaction.
Locating, picking, and packing: This phase is the heart of warehouse operations, where items are located, collected, and packaged for shipment. The goal is to be quick and accurate to minimize delays and ensure orders are fulfilled correctly.
Handling: Effective handling ensures that products remain intact and are efficiently moved from storage to the transportation phase. This step requires coordination and often involves multiple teams to handle the physical movement of goods.
Transportation: After handling, goods are transported to their final destination. This stage must be well-coordinated to ensure timely delivery and optimal route planning, often involving a mix of transportation modes.
Last-mile delivery: The final leg of the logistics process is delivering the product to the end customer's doorstep. The complexity here lies in managing customer expectations and providing a delivery experience that enhances satisfaction and encourages repeat business.
Common challenges in inbound and outbound logistics
Navigating inbound and outbound logistics presents many challenges that affect the entire spectrum of supply chain activities. These challenges can impact a company's ability to manage its supply chain effectively, affecting performance and customer-based outcomes.
- Supply chain visibility: Lack of real-time data can lead to inefficiencies, as businesses can’t track shipments and inventory levels accurately. This can result in overstocking or stockouts and delays in the production or shipment of goods.
- Inventory management: Balancing just the right amount of inventory is essential to develop and maintain any streamlined efforts in a warehouse. Too much inventory ties up capital and increases storage costs, while too little can lead to missed sales opportunities.
Read this for a deep dive into optimizing logistics through time slot management software.
- Transportation management: Fluctuating fuel costs, vehicle maintenance, and regulatory compliance complicate transportation logistics. Selecting optimal routing and transportation modes for cost and time efficiency is equally fraught with surprises and unplanned events.
- Warehouse efficiency: Inbound and outbound logistics rely on efficient warehouse operations. Improper layouts, inadequate equipment, and poor workforce management tactics can lead to unnecessary bottlenecks and delays at your door and on the floor.
A powerful warehouse dock appointment scheduling software to streamline your truck queues and reduce backlog penalties.
- Customer demand forecasting: Predicting customer demand influences both inbound and outbound logistics. Inaccurate forecasts can lead to either an excess or a deficiency of products, which have negative downstream and upstream impacts that interface with your operations.
- Regulatory compliance: Staying up to date and in compliance with international, national, and/or local regulations regarding transportation, labor, and trade can be a persistent challenge—made more difficult depending on where your operations are located.
- Returns management: In outbound logistics, handling returns can be complex and costly. Efficiently managing the return process is essential to maintain customer satisfaction and minimize losses. Customer perception hangs in the balance when a return is requested. Speed, customer service interactions, and many other activities must be aligned.
- Technology integration: Adopting new technologies to improve logistics can be difficult, especially for established businesses with legacy systems. Often, the psychological fear of switching and the failed attempt to accurately consider the long-term value of switching within the ‘cost of switching’ calculations keep companies operating at sub-par standards.
- Sustainability concerns: Increasingly, logistics operations must consider their environmental impact, striving for sustainability in packaging, transportation, and waste management. This can be as much an internal desire as it is a customer demand and expectation. Depending on your materials, goods, or services, this can be a significant factor.
- Cost control: Managing costs without compromising the quality of logistics services is a continuous challenge due to the many variables involved in logistics processes—as we’ve described in this article. Luckily, you can get help optimizing your operations while saving time and money on developing the data and analytics necessary for substantial business insights and decisions.
Check out these 6 important tips to consider when choosing the right logistics partner.
Optimizing logistics for efficiency with GoRamp
GoRamp is an innovative logistics and supply chain management platform designed to streamline and optimize all warehouse, freight, and transportation management activities. By integrating a suite of tools focused on transparency and efficiency, GoRamp significantly mitigates common logistics challenges.
Through its platform, GoRamp addresses the crux of logistics inefficiencies by providing real-time visibility into both inbound and outbound operations. This enables businesses to anticipate and react swiftly to potential delays, manage inventory more effectively, optimize their order fulfillment processes—and so much more.
Its comprehensive analytics empower decision-makers to identify and rectify bottlenecks, ultimately reducing downtime and improving the overall velocity of your supply chain logistics operations.
Inviting companies to revolutionize their logistical approaches, GoRamp offers a strategic service. The platform's dedication to alleviating logistical burdens allows businesses to focus on growing their business, margins, and customer programs.
Let GoRamp be your systems software partner. Schedule a demo today!