Since you are reading this, we assume that you already know what a Dock scheduling platform is and now you are considering if it is truly for you. In case you are not familiar with it, here is a great piece that we did some time ago about what dock scheduling is.
So, you are thinking about getting a Dock scheduling platform but still have some doubts. Will it be a good investment? Is it the right time for your operation to start using a professional Dock scheduling platform? Does my operation even need a Dock scheduling tool and how to choose it?
We have listed symptoms showing when you need a Dock scheduling software, trends indicating its need in the future and signs that it is not for your operation.
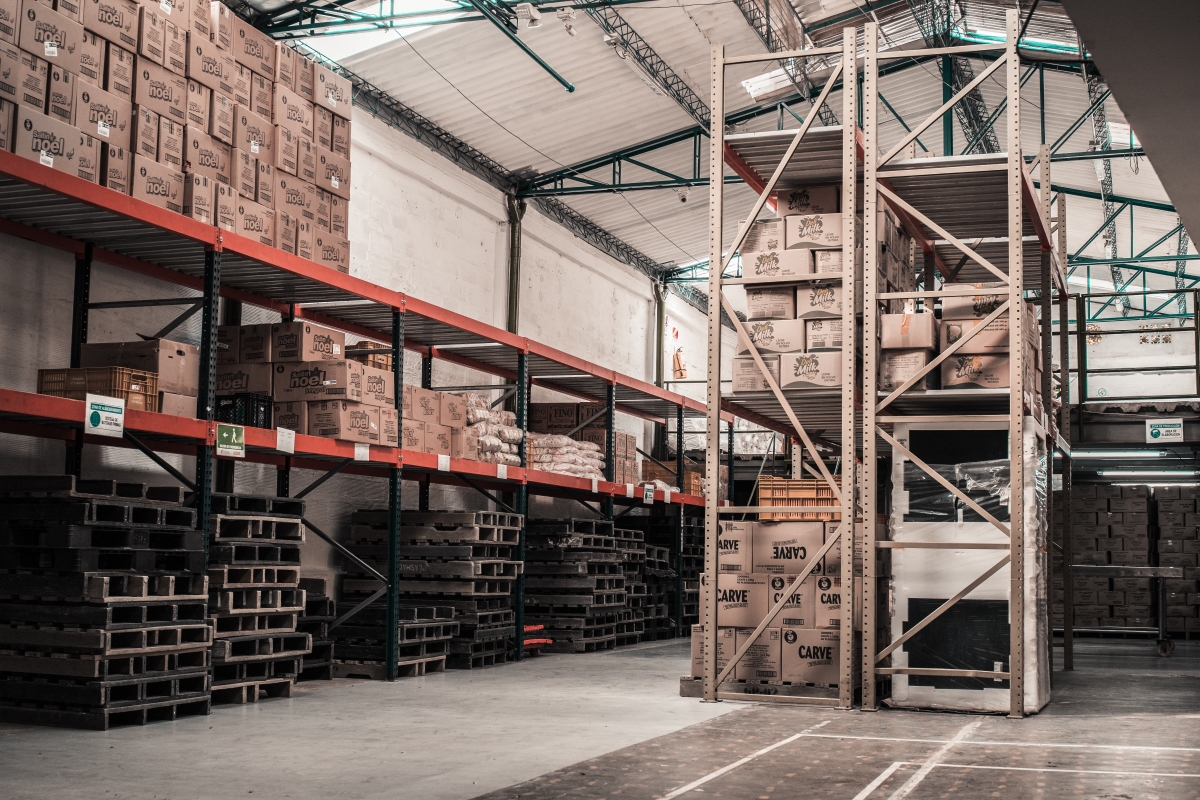
Symptoms Pointing to the Need for a Dock Scheduling Platform
Congested loading ramps. Do you have times when your yard looks more like a truck dealership, with trucks parked on every corner? Congested loading ramps and long truck queues are the number one indication that your operation needs a Dock scheduling platform.
Unhappy drivers and carriers. Unplanned and long waiting times at the warehouse does not make anybody’s life easier. Your warehouse is just one of many stops for a driver that day and carriers usually need to keep a tight schedule.
Penalties and missed cargoes. You receive fines for late loadings, you get penalties from your carriers and you miss cargos due to congestion at the warehouse or insufficient loading capacity.
Limited warehouse capacity. Most warehouses have their loading capacity constraints. Whether it is the number of docks, people, working time or available equipment, any of these constraints can quickly create a small fire in your day-to-day operations.
Most of businesses face a late supply arrivals problem. We have prepared a blog on how to avoid it. Read "How can You Ensure Supplies Arrival on Time?"
Unbalanced workload at the warehouse. Your warehouse spends the first half of the day relaxed and the second half like it is black Friday. Drivers are complaining, time is running out and nothing is done on time. Personnel gets stressed, mistakes start happening and in the end, no one is happy.
Carriers are late. Let’s not forget that truck queues at docks are also caused by carriers that miss their delivery times. It is perfectly fine to be late from time to time, but if it becomes a regular carrier behaviour, you’ll have a constant problem. Analytics from a Dock scheduling platform can be used to identify such behaviour.
Everything is done manually. Non-stop calls, endless spreadsheets and tons of emails to book a dock, inform stakeholders or make last-minute changes. All this manual communication, information entering, and distribution take a lot of precious time and are bound for human errors.
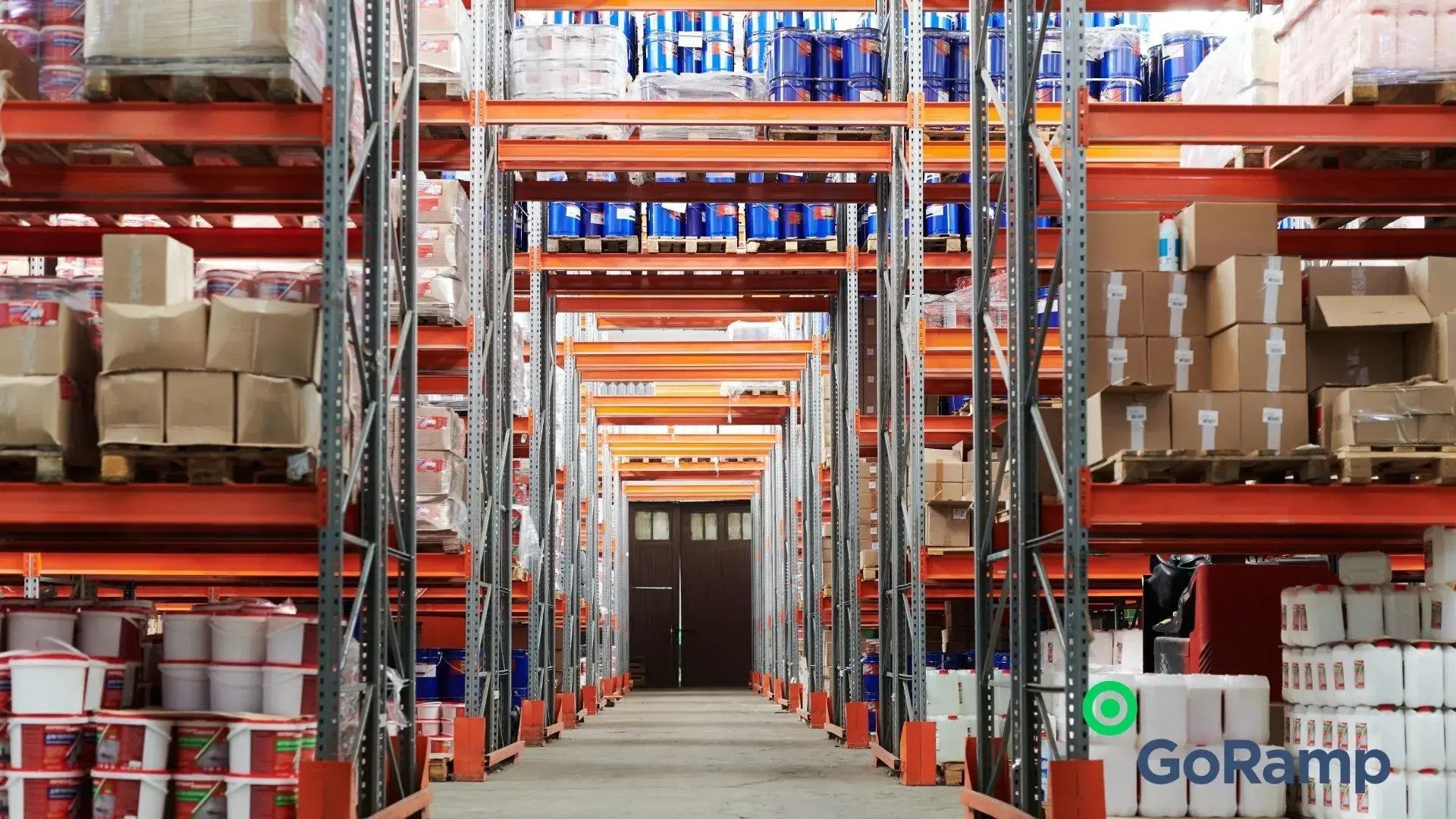
Lack of traceability. When information is mainly stored in emails and paper documents it becomes difficult to look back at past events and analyze them. After a busy day, you won’t have exact information on which truck arrived on time or which carrier was late and disrupted your loading schedule.
To effectivelly plan your dock's processes is not an easy task. We have prepared a blog to help you with this operation: "Checklist: are You Planning Your Docks Smartly".
Trends Indicating a Dock Scheduling Platform Need in the Future
Growing operations. If your production and operations are growing steadily you should already start thinking about getting a Dock scheduling platform. Do you see more trucks coming in and out? Do you have plans to increase your production? Is the number of reservations growing? At some point, the growing number of trucks in your yard will start causing problems that we have covered above. And if not tackled, they can start to interfere with your growth.
Currently using an appointment management system. Between a manual dock scheduling and a dedicated platform, there is the in-between stage - the appointment management system. In practice, it is an online calendar, such as a shared Google calendar, spreadsheet or even Outlook calendar, that are used to schedule truck arrivals and book docks. It still relies mostly on manual management and performs only the basic scheduling functions. Such calendars cannot consider various constraints, lack stakeholder communication features and many other small yet vital functionalities.
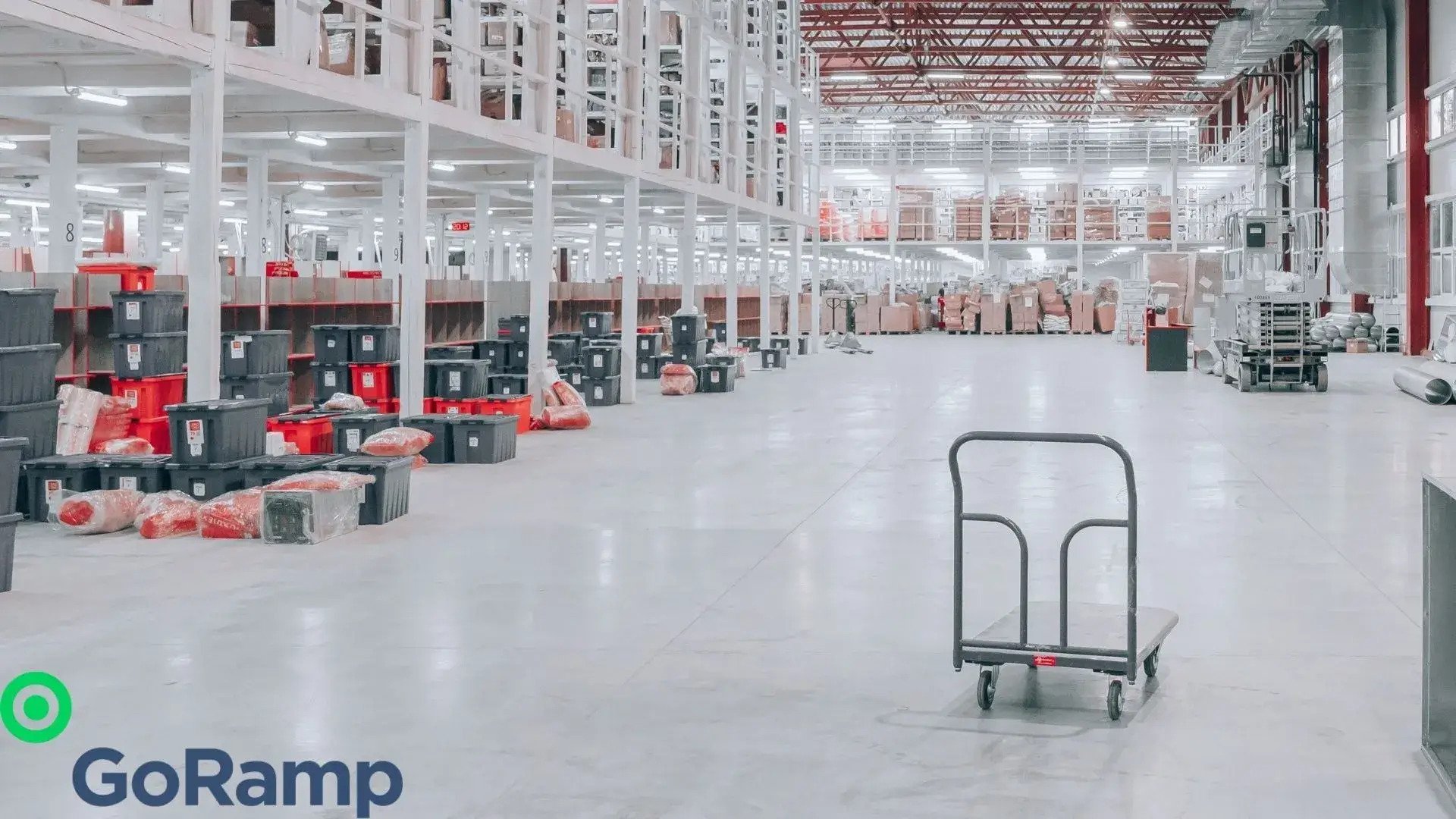
Multiple teams handle delivery information. Inbound and outbound delivery information is often managed by different departments. Supply department is ordering raw materials for production, export team is ordering product shipping to clients and customer support receives information about incoming trucks. All this information and requests need to be smoothly converted to your warehouse dock schedule and prioritized. Doing this without a centralized system is slow, costly and inefficient.
Signs that a dock scheduling platform is not for your operation
Low number of cargoes or reservations. If your warehouse does not receive or ship a lot of cargos, there is a chance that a Dock scheduling platform is not for you. Don’t get us wrong, you could still use a Dock scheduling platform and improve your operations by eliminating certain manual tasks. Our experience shows, that Dock scheduling platform benefits are felt for operations that handle from 10 trucks per day. After all, a Dock scheduling platform is an investment that should pay back for itself after some time.
Just-in-time loading. You have trucks lined up and waiting for your production to manufacture products. Trucks queues happen not because of insufficient loading capabilities or poor organizational processes but simply because there are no products to load. If your products are loaded the minute they are ready, you might not need a Dock scheduling platform. In such a case, the bottleneck is your production and not your warehouse.
Same day production and shipping. You manufacture and ship products on the same day you get the order. This way, you do not know how many orders you will have the next day, when they will be ready for shipping and how many trucks will need to visit your warehouse that day. Using a Dock scheduling platform for this type of operation will require a lot of rescheduling, cancelling or ordering last-minute pickups.
Specific and quick loading process. If your loading process is specific, such as loading truck tankers, or it is fast, simple and takes 5 minutes, then Dock scheduling platform probably won’t make your life easier.
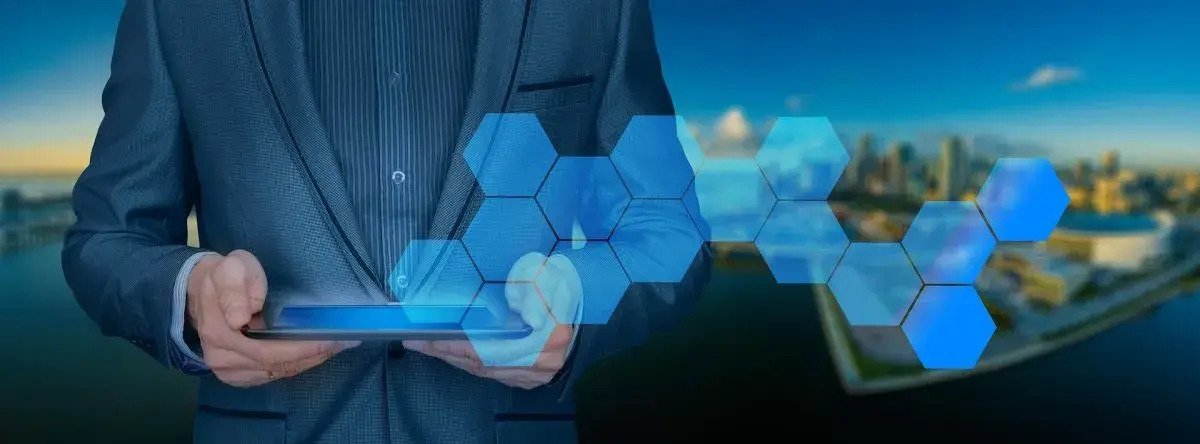
Dock Scheduling Platform - Yes or No?
If you found at least a few similar situations in this article, it might be the time to think about a Dock scheduling platform for your operations. Even if you manage fine without it, over time those situations can develop into something that is actually disrupting your day-to-day operations.
Not all operations need a Dock scheduling platform today but there are certain trends that can indicate its need in the future. We believe that it is better to be prepared in advance for this need than to put out fires when it is too late.
Finally, not all operations can even benefit from a Dock scheduling platform due to their specifics. However, it is always best to talk with an expert and evaluate each case individually.
We are eager to share our expertise with you. Book a quick call with our expert and we will help you to understand how a Dock scheduling software could benefit your business.